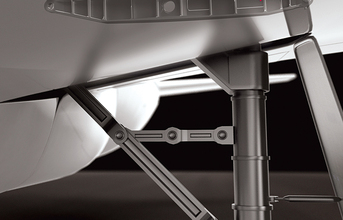
The demand for titanium materials in the aerospace industry is rising. Experts are predicting an average increase of 20 percent over the next five years. This will have consequences for the manufacturing plants, since processing titanium usually requires long machine running times. Walter AG supports its aerospace customers with new tools and extensive knowledge of components. The aim is to manufacture titanium components cost-effectively and in a time-saving manner.
The aircraft industry readily uses titanium, for highly stressed structural components in particular: Door frames, landing gear mounts and wing attachments - all these components typically have a high machining content, it is not unusual for the volume of swarf produced to exceed that of the finished component. This is primarily due to the fact that a large number of pockets are cut from solid forgings. Deep and shallow pockets, 5-axis pockets, triangular pockets - often with very thin walls or bottom faces ; these pose a huge challenge for milling which, logically, is the machining technology for these structural components. Indexable inserts and solid carbide milling cutters help to maintain the balance here. The main focus is on process reliability since these structural components are extremely expensive. At the same time, cost pressure from the market demands high machining and productivity performance.
Typical when titanium machining, the material's low thermal conductivity and its tendency to vibrate require a very rigid machine concept as well as optimum cutting edge preparation. Dirk Masur, Component Manager Aerospace at Walter AG in Tübingen, Germany, together with his colleagues, works with titanium components and their special properties on a daily basis: "We focus on complete solutions," he explains. "This means that we coordinate all aspects, such as the tool design, CAM program and machining strategy, with the application in accordance with best practice considerations." The result is modern tool concepts which, in turn, are matched to the tasks in question, such as roughing, semifinishing or finishing.
(Continued on next page)