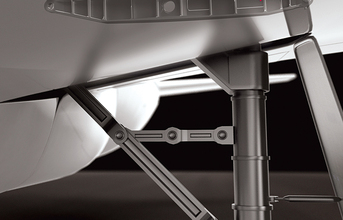
Last but not least, according to Masur, the development of productive and reliable strategies at Walter is based on knowledge of components which has been built up over a number of decades: "Being part of a global network is something we consider to be extremely important. Our expertise is based on intensive partnerships with focus customers, universities and machine tool manufacturers. Together, we are continually
developing the machining operations for key components. This is how we ensure that we are always using the very latest technology."
In the end, the machining specialists from Tübingen provide their customers with bespoke processes which enable maximum machining volumes. The key here is to match the processes with the available machine type capacity, for example, to gain maximum output even from machines with a lower performance. "The machining operations are simulated and verified before the handover," Masur stresses, "this means that the user does not have any unpleasant surprises in terms of cost-effectiveness or process reliability."
Representative test in titanium
Since there are virtually never any real test components readily available in the world of aerospace, nor any large structural parts, the experts at Walter AG demonstrated the performance of their current tool generations on a generic component. This is made of the commercially available material Ti6Al4V (3.7164). The experts at Walter designed the component with a range of typical pocket shapes which are the same as or similar to those which can be found on real components. This means that the machining results can be transferred one to one.
The plan includes a task for a quartet or tools: The M3255 tangential porcupine milling cutter, the M4002 high-feed face milling cutter (roughing operations), the Ti40 solid carbide end milling cutter and the modular ConeFit variant with Ti50
changeable head (semi-finishing and finishing operations). This is a combination which is possible in reality, for example when machining landing gear mounts. The coatings, as well as the macro geometry and micro geometry of the two solid carbide tools are designed specifically for titanium machining. The M3255 and M4002 milling cutters were given indexable inserts made from the new Walter WSM45X cutting tool material. The extremely tough CVD coating is ideally suited to
ISO S and ISO M applications.
(Continued on next page)