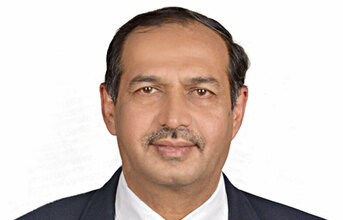
BC Rao, Kennametal
Last year
Our business is primarily associated with the manufacturing sector and related industrial production index, and the growth in manufacturing for the last year has remained moderate, with slight and weaker improvement of business conditions across the country's goods manufacturing sector.
Customer segments
In India, the majority of our business comes from the industrial markets. Its established base is a compelling attraction for global manufacturing OEMs. This trend is likely to continue in the coming years too and we see a strong growth in this sector including on export opportunities and local in-country economic growth. We have also expanded our product portfolio with technologies from acquisitions that offer differentiating products and services for additional markets including energy.
Addressing customer needs
It is evident that cutting tools contribute roughly four to five percent of the total manufacturing cost. Nearly 40 percent of the component manufacturing cost is associated with machine tools and cutting fluids contribute around 12 percent.
Hence, right selection and application of cutting tools are very important not only to reduce the tool cost, but also to improve productivity helping to address the overall manufacturing cost. We are constantly engaged in communicating the productivity savings we bring to customers through ‘Process Optimisation Programs' (POP). We can deliver better value savings to customers through this technique by optimising the process parameters. Our application team will engage with key customers and identify the production bottlenecks. It is done in a systematic manner which starts with a detailed survey of the line, maps existing process and documents the areas of improvement. At the end of the study, key findings are shared with the customer and the Kennametal Process Optimisation team will propose a new set of tooling solutions for improved performance.
Delivering quality products
We produce thousands of products, both standard and custom solutions, and we have quality deeply rooted into our management operating system globally. We also invest back into our business to make sure we have the best equipment and facilities to deliver products to our customers.
Environmental and safety concerns
Kennametal follows strict Environmental, Health and Safety standards throughout its global operations and, as part of the company's Protecting Our Planet commitment, we continually focus on improvements in energy and water conservation, materials recycling, waste reduction and other practices consistent with our tradition of responsible environmental stewardship. Minimum Quantity Lubrication (MQL) technology is the process of applying the lubricant required for cutting exactly in the interface between the cutting tool and work piece.