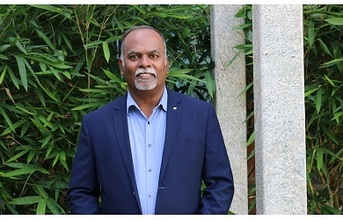
How would you analyse the role of Industry 4.0 in the New Normal with the Covid19 outbreak?
The COVID-19 pandemic has triggered large scale digital transformation across industries and the globe. This creates new opportunities to implement innovative digital strategies and rapidly embrace Industry 4.0 technologies. They are instrumental in augmenting smart factories and mitigating disruptions in the supply chain.
For example, in the ‘new normal', sensors integrated with Internet of Things (IoT) can be used to enhance supply chain visibility. They will be able to track parts or products throughout the supply chain to enable remote monitoring and increase accountability. The data from these sensors can be used to create actionable insights that can help businesses make well informed decisions with respect to their processes and customers.
These technologies can also help bolster the overall resilience of businesses and are great tools for speed, reliability and data-driven decision making.
Technology trends like big data, cloud, mobile and Internet of Things (IoT) are propelling the industry towards a paradigm shift in terms of a digital transformation. Adoption of these trends is making factories ‘Smart'. So how are these trends influencing the factory environment across different functions like design, development, production, marketing & sales, delivery and services?
Industry 4.0 has an impact across all functions and processes of a factory and its operations. It creates a focus on data-driven innovation across processes and product lifecycle. In the initial stages of product design and development, computer-based designing and 3D printing can be used to create prototypes quickly and eliminate the need for a trial and error method which used to be a long-drawn process in terms of time, energy and resources. The overall production can be streamlined through a smart supply chain that creates leaner processes. Companies can also leverage 3D printing to showcase the products to potential customers and in few cases investors. In the future, other technologies such as Augmented Reality (AR) and Virtual Reality (VR) can also play a key role in expanding their capabilities. IoT enabled sensors can also be used to track parts or products during the final delivery stage to ensure that it reaches the right customers and on time.
What role will ‘Smart Factories' play in the success of ‘Make in India' initiative, which aims to transform India into a global manufacturing power?
The pandemic has created new realities for the manufacturing sector. With the world leaning towards Asian countries to fulfil manufacturing requirements, India currently has a unique opportunity to strengthen its presence as a manufacturing powerhouse.
In line with this, the Indian government has been strongly driving this vision by promoting ‘Make in India' and announcing favourable economic packages and creating an investment friendly environment. The future will be defined by connected smart factories with the agility and capability to handle new customer demands. Besides streamlining the supply chain, Industry 4.0 technologies implemented in these smart factories can also help provide actionable insights and increase overall efficiency and hence energy savings.
The gradual shift to smart factories will poise India to leverage global competencies and transform existing standards of manufacturing.
Will ‘Smart Factories' mean sustainable and ultra-efficient production lines that require little or no human intervention? Will it mean increasing automation and robotics at the cost of human jobs?
Every industrial revolution has introduced a new set of technologies to the workforce. Technology has also enabled employees to deliver better. As Industry 4.0 technologies such as advanced analytics, IoT, AI, cognitive automation and others grow exponentially, it is expected to reduce redundancies in the supply chain by automating or streamlining specific processes. This also means that there is a need for a highly skilled workforce with the right competencies to handle the technologies and increase the pace of its adoption.
However, the manufacturing industry's biggest challenge today is the widening skill gap. Future workplaces must be prepared through skilling initiatives to successfully leverage industry 4.0 technologies and transform businesses. Existing workforce can also be upskilled or reskilled to improve their competencies.
Today, consumers can provide feedback directly to manufacturers through various digital platforms. How can a ‘Smart Factory' make the most of this information?
Manufacturers are working towards continuous improvement and innovation by integrating customer feedback as part of their process. Data analysis is a core element of a smart factory and it can be used to understand customer requirements, optimise processes and improve transparency.
Grundfos' SmartServ Service App is one such easy to use application that provides manufactures to help monitoring their products and tracking the same. The SmartServ will provide an option of getting Service Support for Grundfos products, besides the current traditional medium i.e. phone calls & email. We aim to provide prompt and efficient service to resolve any issues with Grundfos pumps, reducing the service processes and minimising the downtime due to any repair works. Through this app, one can contact Grundfos or locate the nearest service provider, fill in the details and raise a service request with the option to attach a picture of the pump/system which is geo tagged. This app also helps the senior management team track and monitor the status of every complaint and step in when needed to ensure customer delight.
How will a ‘Smart Factory' adopt to the evolution from simple ‘product development' to disruptive innovation'?
The fourth revolution has digitized the manufacturing processes and revolutionized product development. It has empowered organizations to create smart products that successfully leverage technologies such as IoT at every stage of development.
For example, 3D printing can be used during initial stages of product development to provide proof of concept or protypes. At Grundfos, we currently use 3D printing to create prototypes. It helps us work with new materials and make complex components for the actual products that will help improve its performance.
About 30 years ago, it would have taken 4-5 weeks to make a prototype at the product development stage. Around 20 years ago, we could create prototype in 4-5 days and currently smart factories have helped us create prototypes in 4-5 hours. That explains the transformation that digitalisation has brought about to our industry and across many manufacturing industries.
3D Printing has the potential to further disrupt the manufacturing value chain. How does a ‘Smart Factory' view this rapidly growing phenomenon?
Besides optimising product development, 3D printing has a positive impact on all other stages of the manufacturing value chain as well. They can be used to manufacture parts or products cost efficiently with a reduced production time and improved precision.
They are also an effective tool for companies to use prototypes and illustrate product functionality. This helps not only to secure orders before the final product is manufactured but to also attract investors at the initial stage of product / concept development.
Additionally, 3D printing helps optimise the supply chain by reducing the need for a large inventory by introducing on-demand manufacturing and increasing overall flexibility to new changes.
Can the ‘Smart Factory' optimise the supply chain for a win-win situation?
The supply chain is a crucial dimension of a smart factory. Digital transformation will help create leaner supply chains with optimised processes. Sensors along with IoT can be used to further improve transparency at each level of the supply chain while predicting potential bottle necks and automating redundant processes.
In the long run, an intelligent supply chain will be able to boost the efficiency of smart factories by embracing new technologies, improving responsiveness, strengthening resilience and delivering better business outcomes.
We have been able to optimise our global supply chain through a partnership with SAP. SAP APO interacts with SAP ERP to create an integrated platform that helps us with our overall sales plan and operational planning. This is integrated across levels and geographies to ensure immediate intervention in case of any adjustments. We have been able to surpass customer expectations through this transformation by cutting lead time and improving overall delivery time by 10-15 percent.
It will be relatively easier to build Greenfield ‘Smart Factories'. But how can Brownfield plants - particularly with bigger scales and complexities - become ‘Smart'?
While it is easier to get a Greenfield project to be a Smart Factory from the planning stage, there is no barrier in also making brownfield plants smarter. Key elements here are planning, implementation and monitoring. There will be a requirement to upgrade the infrastructure - but this in the long run will create savings. Companies have to consider the life cycle costs rather than just initial investment costs here.
The first step of this transformation is to identify isolated equipment and improve its overall efficiency and connectivity by integrating IoT or upgrading its existing IoT network. This means that the aging infrastructure and machinery in these plants should also be upgraded to adopt intelligent and sustainable technology. Digitalization of these components will also help in remote diagnostics to understand if there is going to be any critical equipment failure ahead of time and ensure preventive actions in time.
END