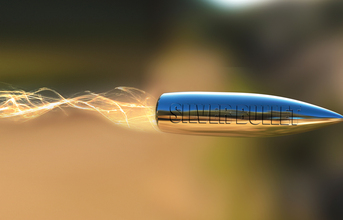
Most discrete manufacturing plants struggle with maintaining good on-time delivery performance. Consistent on-time performance of high 90s (sticking to committed deadline) is extremely rare.
In fact, many organisations have "built-in" low reliability in their commitments; they commit in wide ranges of delivery lead-time or use monthly or weekly buckets to measure delivery performance. Few have the ability to commit to a date and meet it. (The best way to validate this hypothesis is to check the level of skew of dispatches or order completion in a month or a quarter for long lead-time environment.)
If the order arrival is erratic throughout the month, we expect the due dates to be staggered across the month. However if most of the order completions are skewed towards month or quarter end, it is a sign of poor on-time performance. Skewed completions of orders or dispatches during month-end or quarter-end are an industry wide epidemic).
The real challenge of maintaining high on-time performance in discrete job shops is meeting different objectives, which at times, conflict with each other. The need to maintain high on-time performance can come in the way of ensuring maximum capacity utilisation from the critical work centers.
Evolution of MRP (Material Resource Planning)
Academicians, consultants and plant managers have been dealing with the problem for decades. Attempts were made with MRP, MRPII (also called Manufacturing Resource Planning) and later with Advanced Production Schedulers or Optimisers (APS or APO) to solve the problem.
Each solution tool was designed with limited understanding of the underlying problem. The solutions were also "biased" based on the capability in computing technologies, available at that point of time.
When MRP was invented, it seemed like a panacea for all ills in manufacturing. With the available computing power, one could do a batch process and convert the independent end product demand to demand of dependent components after netting off the available inventory.
The "pre-fixed" lead-time of each stage can be used to calculate the due date, and derive the corresponding production or procurement schedule. By touching just a button, one could get to know what "dependent demand" components need to be manufactured/procured, in what quantities and by when. One needed to just meet the intermediate due dates of components processing to meet the final due date. This seemed like a breakthrough for managers trying to do the same manually wherein the efforts were not only time consuming but were prone to human errors.
While the logic of just using a fixed lead-time to schedule procurement orders was reasonable, it is not suitable for a manufacturing system as it is an erroneous assumption. The capacity usage by loaded orders has an impact on lead-time of new orders. Hence one could not use a fixed lead-time to schedule as doing so would imply that the capacity is being completely ignored.
(article continued on next page)
The author is Director, Vector Consulting Group.