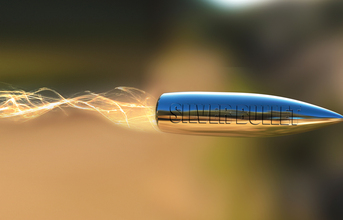
The Theory of Constraints Approach
The way to maintain reliability is to have stability in the due date scheduled; variability should not force change in schedules. This required one to keep aside protective capacity while scheduling, which means, practically, there should be only one constraint in the plant.
Having many constraints will force one to keep buffers in many places with low overall output of the plant. So with a capacity buffer on the single constraint resource, one could get a schedule that stays stable without trying to have buffers in many resources. This approach can ensure one has the maximum output from the plant as a whole while maintaining a stability of due dates.
This means that other limiting conditions (or constraints) have to be removed. This may seem like an impractical idea due to potential investment required. However, in most plants, various visible "multiple constraint" problem is more of a symptom than a real problem. An environment of very high WIP in a plant can create temporary bottlenecks in many work centers.
At the same time, it could also lead to cases of artificial material shortages due to diversion of common material used across orders. When there is lot of WIP, and every work centre is driven by utilisation/efficiency, each work centre "cherry picks" components across orders. Also, the consideration for "cherry picking" is different for different machines. As a result production lead-time goes up and order reliability becomes extremely poor. This unreliability creates urgencies/fire-fighting in the plant due to late orders. Urgencies create additional set-ups creating multiple bottlenecks leading to low plant output.
As a first step towards removing the symptom of multiple constraint and associated chaos is to reduce the WIP, and forcefully maintain the WIP at a constant low level. With low WIP, the opportunity to "cherry pick" orders is limited as there are few orders on the shop floor. However, very low WIP can lead to starvation and low output. The way to check if one has excessive WIP is to compare the touch time of an order with the total production lead-time. If the touch time is less than 10 percent of the lead-time, and if there is day-to-day fire fighting with frequent requests for expediting, the WIP is definitely high.
In such an environment, halving the WIP does not lead to starvation. Reduced WIP along with a priority system focused on order completions prevents wastage of capacity and the output of the plant goes up. At the same time, with reduced WIP, the real constraint is revealed. As part of the solution, a constant reduced WIP is maintained before the constraint resource. All other resources subordinate to ensure there is no starvation at the constraint resource.
The material release to the plant is based on the WIP maintained. So, if the output of the constraint resource falls (due to uncertainty or product mix changes), further material release is stopped to maintain the WIP. Similarly, if the output of the constraint resource increases (due to no murphy or favourable product mix), material release is increased so that there is no starvation at the constraint. In other words, WIP is maintained.
This mechanism of "pull system" of using constant WIP ensures maximum utilisation of the constraint resource without the need to precisely define capacity in the planning phase. At the same time, one could leave behind a buffer capacity in planning (while quoting due dates) without any fear of losing it in execution. This would also ensure that the reliability of orders goes up.
In a plant where reliability (i.e. order due date performance based on initially committed dates) is extremely high, there is no need to follow the concept of a planning horizon or the bucket system of planning. One can follow a system of daily perpetual planning of new orders, without following the planning bucket (or horizon) system for rescheduling based on observation of past period performance. The concept of daily perpetual planning also ensures high utilisation throughout the month.
In some manufacturing plants, there can be cases of interactive constraints due to drastic changes in product mix. The only way to solve this problem is to ensure that orders are throttled in planning as well as releases to ensure constraint stays at one single place both in planning and execution. In the long run, it pays to elevate such temporary bottlenecks to ensure a stable plant.
The execution based pull system of Theory of Constraint takes away the need to be "perfect" in planning. The silver bullet in manufacturing systems lies in the approach of "good enough" planning (schedule with capacity buffers) coupled with a perfect execution by the way of controlling WIP every day.
The author is Director, Vector Consulting Group.
END