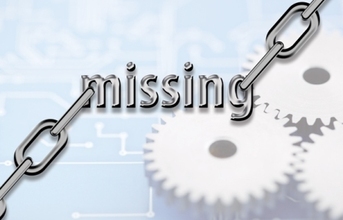
India's biggest drawback has been our poor infrastructure and acute shortage of power. Adding to this is the lack of enabling factors like incentives in the form of cheap land and tax benefits. Further, regulatory hurdles like environmental clearance, which lead to delays in approvals. India needs to push its massive and ambitious plan for US$ one trillion infrastructure investment to develop power, roads, ports and civil aviation during the Twelfth Plan.
Currently, there are really big projects underway such as the Delhi-Mumbai Industrial Corridor, entailing over US$ 90 billion in investment, with nine mega industrial zones, high speed freight lines, three ports, six airports, a six-lane intersection-free expressway connecting the two big metros and a 4000 MW power plant. The government must have more faith in the private sector if it needs these huge infrastructure projects to be completed in time and with quality. It needs to provide support in terms of easy processes, land availability and better finance options.
Rigid labour laws also constitute as a major bottleneck in making India a globally attractive and competitive manufacturing hub. The archaic labour laws in India have been instrumental only in breeding informal, low-wage employment. Compounding this is the attitude of some labour unions which are politicised and whose aggressive stance works inimically to the interests of not only the organisation but even the labour itself which they represent.
The myopic labour laws and a stifling industrial environment are major hurdles in promoting manufacturing sector. The answer lies in bringing major labour reforms based on collaboration and engagement rather than conflict.
Industries like textiles and apparels that are labour intensive account for only 13 percent of gross value added in organised manufacturing. Most of these units employ less than 10 employees while 90 percent of Chinese textile employers have more than 50 employees. Although, instituted to ensure labour welfare, the one-sided laws make employment contracts perpetual -- the corporate equivalent of marriage without divorce, forcing industries to move towards capital intensive manufacturing.