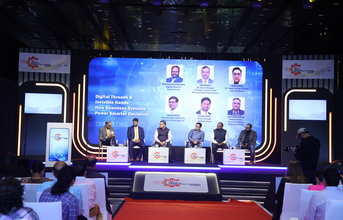
Digital Threads Panel
In an age where manufacturing is increasingly driven by intelligence, integration, and immediacy, the concept of the "digital thread" is fast becoming the hidden force weaving disparate functions into cohesive, high-performing systems.
During a recent panel discussion at the ET Now Machinist Tech in Manufacturing summit, which was moderated by Sudhanshu Mittal, Head and Director of Technical Solutions at the MeitY NASSCOM Centre of Excellence (CoE) for IoT and AI, an important point was raised: "In smart manufacturing, continuity is everything," stated Sudhanshu Mittal. "It's about how one activity hands over to another, how data flows, and how every outcome feeds into the next action. Traceability began in Industry 4.0—but in 5.0, it's being humanised, contextualised, and made seamless."
The panel brought together seasoned leaders across multiple sectors of the manufacturing value chain, each shedding light on how digital threads are revolutionising their domain, not just in technology, but in mindset and execution.
The Product Life Cycle as a Living Thread
Deepak Manvi, Product Manager at Hoffmann Group, was the first to outline the practical application of digital threads from a product management perspective. "From design to development, launch to feedback, the data we capture becomes the backbone of all decision-making," he explained. "It's not just about tracking; it's about constant calibration. We use tools like the ADL Matrix to determine where a product stands in its lifecycle and what action is required—be it testing, marketing or redesign."
Manvi stressed the importance of customer feedback loops, saying that digital integration allows every function—from R&D to customer support, to work from a single, evolving source of truth. "This is what enables agility and longevity."
Where Precision Meets Productivity
Rajeev Mittal, CIO at Endurance Technologies Ltd., highlighted how digital threads are transforming operations at scale in the automotive sector. He underscored the value of digitalisation in streamlining decision-making and achieving operational continuity across the enterprise.
Vipan Singla, Vice President – Head of Design & Quality at Lava International, added a complementary dimension from the mobile manufacturing space, "For us, digital threads aren't limited to traceability—they are the control tower for the entire development lifecycle," he noted. "From design inception to mass production, our digital framework enables complete control over time-to-market, agility in design, and synchronised manufacturing."
He emphasised that end-to-end digital control is no longer a luxury; it's the bedrock of timely, cost-efficient, and competitive product development in today's market.
A Strategic Backbone, Not Just Technology
For S Aravindan, CIO and General Manager – IT & Digital at Larsen & Toubro's Precision Engineering & Systems division, digital threads represent far more than a set of tools, they are a strategic enabler.
"The digital thread is not a technological initiative—it is a strategic one," he stated firmly. "It connects every function across the value chain, from design to production to service, and ensures real-time, contextual data is available to every stakeholder in the format they need."
According to Aravindan, the greatest impact of the digital thread is on the shop floor. "It is where data turns into action, where precision meets productivity, and where digital investments are translated into measurable outcomes."
When asked about the challenge of integrating IT and OT in a project-heavy engineering environment, he acknowledged the complexity. "This is not a one-time project. It's a transformation journey. At L&T, we have developed a digitally integrated ecosystem, connecting engineering complexity with real-time execution through secure, seamless data flows."
Aravindan shared that they followed an 8-step approach, starting with aligning digital transformation to strategic goals, eliminating data fragmentation, and building a secure digital infrastructure.
"We integrated our PLM and ERP systems with project management and IoT sensors to create a closed-loop intelligent feedback system. This is how we ensure decisions are precise, proactive, and secure."
Connected Workflows, Actionable Insights
Shitendra Bhattacharya, Regional Director at Emerson Test and Measurement, reflected on how digital threads are changing not just systems, but culture: "For us, the digital thread is a connected workflow of data across functions. It's not just traceability, it's about contextual insights at every touchpoint," he said.
Bhattacharya emphasised the shift from reactive to responsive culture. "This approach allows for better decision-making, improved product quality, and accelerated innovation. It's about moving from ‘what happened' to ‘what's next'."
Seamless Synchrony Across Supply Chains
Rajeev Mittal, Chief Information Officer at Endurance Technologies Ltd., offered a glimpse into how Tier-1 auto component manufacturers like his are weaving together digital systems across the value chain. "We have built a centralised, integrated IT ecosystem that connects not just our internal processes—from PLM to ERP, CRM to IoT, but also extends to our partners on both the customer and supplier sides," he said. "This ensures that when demand fluctuations occur, everyone—from the shopfloor to subcontractors—has visibility of inventory and production status in real-time. There's no room for shadow systems, our focus is on a single source of truth."
The integration allows Endurance to stay agile in the face of disruption, a feat they are now enhancing with AI-driven forecasting, generative AI pilots and predictive maintenance models. "Deploying AI doesn't guarantee immediate returns, it requires data maturity, cleansing, and massaging, but we are committed to this journey," Rajeev Mittal added.
Speed-to-Market and Data-Driven Design
In the ultra-competitive consumer electronics sector, rapid prototyping and agile product development are key differentiators. Vipan Singla, VP – Head of Design & Quality at Lava International, revealed how the company uses data to streamline product iteration and manufacturing. "From industrial design to hardware, every stage is digitally mapped and controlled," he explained. "This ensures a first time-right approach, minimising costly rework and accelerating time to market."
He emphasised the importance of being responsive to evolving consumer behaviours. "Customer preferences change quickly, and our systems must aggregate these shifts and reflect them in real time—from concept to execution."
Data as a Strategic Asset, Not Just QA
For manufacturers, testing is no longer confined to quality assurance. As Shitendra Bhattacharya, Regional Director at Emerson Test and Measurement, put it: "Test data has transformed from a post-production metric to a strategic asset that drives design, process control, and supply chain agility."
He broke down the shift into three layers:
-
At the engineering level, test data is sent upstream to R&D and design teams, enabling smarter and faster product iterations.
-
On the shop floor, it integrates with MES systems to trigger automated alerts for parameter shifts and yield issues—ushering in adaptive manufacturing.
-
From a supply chain perspective, test data helps with supplier quality analysis and recall prevention, supporting informed sourcing decisions.
"The future lies in autonomous orchestration engines, systems that can reroute workflows, sequence tests, and optimise decisions without human intervention," Shitendra Bhattacharya forecasted.
Managing Complexity at Scale
For Deepak Manvi, Product Manager at Hoffmann Group, the challenge lies in managing complexity of scale, product diversity, and regulatory frameworks. "We handle over 60,000 articles daily, ranging from tools worth Rs 50 to machines worth Rs 50 lakhs. Each product category—be it electrical, textile or mechanical—has distinct compliance, import and logistics requirements," he said.
By digitising logistics and integrating feedback loops from customers back into product design, Hoffmann ensures continuous product improvement and timely delivery. "AI-enabled systems, such as our measuring microscopes, now capture component dimensions, porosity, and irregularities in real-time, ensuring a first-right-time manufacturing approach," he added.
From Proactive Problem-Solving to Predictive Intelligence
S Aravindan, CIO & GM, IT & Digital at Larsen & Toubro's Precision Engineering & Systems division, highlighted how they are moving from reactive problem-solving to proactive orchestration. "Our platform automatically generates work authorisations from design to production," he said. "A 3D drawing gets linked to the bill of materials, undergoes inspection, and any deviations—say from CNC machines, trigger real-time alerts via AI models. That's how disruptions are flagged early."
He believes that the future will be shaped by data-driven cultures and smart ecosystems. "We must transition from traditional to smart factories by design, embedding digital twins, robotics, and automation from day one."
Cultural Shifts and Leadership Buy-In
When asked about the one shift—technological or cultural, that organisations must embrace to future-proof themselves, the panellists converged on one answer: culture must change before technology can deliver.
"Organisations must treat data as a strategic asset," asserted Shitendra Bhattacharya. "Move from firefighting to foresighting."
Vipan Singla agreed, calling for top-down cultural transformation to drive proactive data utilisation. Deepak Manvi echoed the sentiment: "The focus should be on setting robust processes first, and then digitising them—whether it's design, procurement or ordering."
Aravindan summarised it best: "Unless cultural and technological intelligence fuse together, we cannot convert our factories into truly smart ones."
Conclusion
The digital threads connecting every node of today's manufacturing ecosystems are increasingly intelligent, increasingly autonomous. And while these threads may be invisible to the naked eye, their orchestration is anything but passive. They act, alert, analyse and anticipate—making data not just a witness to decisions, but their engine.
The invisible hands of real-time systems are not just shaping how factories respond, they are defining how they think. And in that lies the promise of smarter, seamless manufacturing.