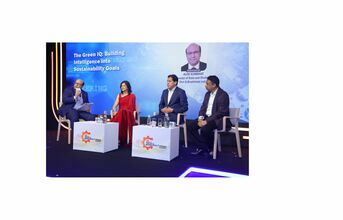
In today's manufacturing landscape, sustainability has evolved from a buzzword into a non-negotiable mandate. Across industries, forward-looking companies are embedding intelligence into their environmental strategies—what is now being coined as "Green IQ."
At a recent thought-provoking panel titled, The Green IQ: Building Intelligence into Sustainability Goals, industry leaders from recycling, pharmaceuticals, and water technology shared powerful insights on how data, automation, and digital foresight are transforming traditional sectors.
Opening the discussion, Alok Kumbhat, Director of Data and Strategy at Dun & Bradstreet India, underscored the importance of intelligent sustainability. "Green IQ isn't just about being sustainable—it's about being smart and measurable in your sustainability efforts," he remarked. "From AI-driven recycling to water molecule engineering and pharma's energy tracking systems, the message is clear—green must also be intelligent."
Reflecting on the company's origins, Dr Vivek Tandon, Founder of revalyu Group, said, "We were set up 15 to 20 years ago to change the way we recycle plastic and PET. Our breakthrough came when we could achieve the same quality as virgin PET—at 10 to 15 per cent cheaper." Based in Nashik, revalyu now recycles over 64 million plastic bottles daily. Yet, as Dr Tandon pointed out, this is still "a tiny drop in the ocean" given that cities like Delhi alone generate approximately 45 million bottles each day.
For revalyu, Green IQ is anchored in four core pillars: traceability, process optimisation, predictive maintenance, and AI-led insights. "The ability to trace where every plastic bottle comes from and ensure it goes through ethical, efficient processes is central to our mission," Dr Tandon explained. With the help of IT and blockchain, the company ensures that its raw materials are free from child labour—a critical condition set by global clients. But technology's role doesn't end there. "Our last plant ran for 680 days with zero shutdown using predictive maintenance software," he noted, crediting AI with optimising energy use and boosting operational uptime.
Taking circularity a step further, revalyu is now piloting scannable product-level traceability. "Imagine walking into an Adidas store, scanning a garment with your phone, and seeing the lifecycle of the PET—from collection to yarn production," he said. "Eventually, we want every plastic bottle to have that same traceable transparency."
The impact of automation at revalyu has been nothing short of transformative. "In our first plant, we processed 4 million bottles a day with 200 people. Today, we process 45 million, with just seven employees," he revealed. The company's zero-liquid discharge facility operates on a closed-loop model that uses 86 per cent less water and 90 per cent less energy than conventional PET production. "We didn't begin with cost in mind," Dr Tandon emphasised. "We began with a goal, to be the most sustainable and CO₂-efficient PET producer in the world. The cost savings followed."
Turning to the pharmaceutical sector, Dr Bikash Kumar Nayak, Site Head Operations and Vice President at Aurobindo Pharma, shared how digital solutions are being harnessed to minimise environmental impact. "Globally, pharma contributes about 4.4 per cent to carbon emissions," he noted. "With 30 per cent of prescription drug production happening in India and China, the industry's carbon commitments are non-negotiable."
Aurobindo has rolled out Energy Management Systems across 49 sites worldwide, yielding savings of Rs 10 lakhs per month per site. Water recycling and reuse have led to an additional Rs 3–4 lakh monthly saving, with no treated water discharged externally. These initiatives are underpinned by data-led automation, which ensures compliance with stringent USFDA and MHRA regulations while optimising resource usage. "Many view compliance as a cost," Dr Nayak remarked, "but if seen through the right lens, it can become a driver of profitability."
Moderator Alok Kumbhat, Director of Data and Strategy at Dun & Bradstreet India, then delved deeper, asking Dr Tandon how revalyu had built a model to convert PET bottle waste into high-performance products. "I'm not sure if we fit under Manufacturing 4.0 or 5.0," Dr Tandon said with a smile, "but our approach has always been about making our processes more sustainable through technology."
Sharing progress over time, he added, "From every 1,000 kilogrammes of PET waste, we now get 970 kilogrammes of usable product. That's just 3 per cent wastage." It's a journey that took seven to eight years, enabled by a scalable chemical glycolysis process. "Unlike mechanical recycling, chemical methods scale faster and at lower marginal cost," he noted.
When asked about the financial and regulatory benefits of digitalisation, Dr Nayak pointed to the power of IoT and track-and-trace systems. "These systems are vital, not just for efficiency, but to pass critical audits. A shutdown due to audit failure could cost us dearly." IoT-driven systems have also enabled just-in-time production, cut inventory costs, and reduced utility bills by nearly 30 per cent.
Offering a fresh perspective, Ameeta Nehra, Vice President – Corporate Strategy at Nanobubble India Co., introduced the concept of "intelligent water." Her company specialises in nanobubble and nanoglobule water technologies aimed at enhancing water's natural properties. "Our aim is to make every litre of water more intelligent," she said. Nanobubble India's patented oxygen nanoglobule water improves endurance, reduces fatigue and boosts physiological performance. But its real value lies in applications like wastewater treatment and agriculture. "We are addressing stubborn metrics like BOD and COD in effluents and reducing pesticide use while increasing crop yield," she explained. These advances are particularly impactful in sectors like aquaculture and rice farming, both of which are highly water intensive.
Commenting on the rising digital expectations of clients, Nehra added, "It's no longer enough to deliver outcomes. Clients want real-time analytics—data on energy usage, chemical dosing, and per-kilowatt savings. Thanks to IoT, our machines can now make those decisions themselves."
On the topic of talent acquisition, Nehra stressed the importance of early engagement with academia. "We work closely with PhD and M.Tech students during their studies. By the time they join full-time, they are already attuned to our culture and innovation agenda."
When the conversation turned to gender diversity, Nehra spoke with palpable conviction. "This is deeply personal to me. I serve as a brand ambassador for WIMA – Women in Manufacturing & Alliance Sector. Our mission is to upskill and enable one billion women to become employable by 2030." She shared a poignant anecdote about her daughter, an AI engineer who interned in manufacturing. "A CNC machine doesn't care about gender. It's society that does and that needs to change."
Dr Tandon wholeheartedly agreed. "About five to six years ago, we introduced a minimum representation policy for women across all departments—from engineers to electricians. It took time, but it worked. Inclusion must be operational, not just a PR line." He added with pride, "In nine years, we have only lost two employees. In an industry where churn is 8–12 per cent, we are under 0.01 per cent. Why? Because Gen Z doesn't just want a job, they want purpose."
As the session ended, Kumbhat posed a final question: Which underutilised digital innovation could revolutionise Indian manufacturing in the next three to four years?
Dr Nayak envisioned a future dominated by AI and 3D printing, where pharmaceutical companies could produce personalised medications and even predict diseases years in advance. "It's not science fiction, we are actively working on it," he confirmed.
Dr Tandon, meanwhile, called for a paradigm shift from the shop floor to the boardroom. "Sustainability must go beyond buzzwords and dashboards. It needs to be embedded into the DNA of leadership. Today, we trace where our products come from. The next step is to trace where they go, that's true circularity."
Nehra concluded with a bold outlook for predictive water management. "Machines will soon know when to start and stop operations without human input. That gives people the freedom to focus on strategy, empathy and innovation. That's the future we are building."
In summing up, Alok Kumbhat aptly remarked, "The future of manufacturing isn't just smart—it's sustainable, inclusive, and deeply human. Green IQ is not only a metric. It's a mindset."