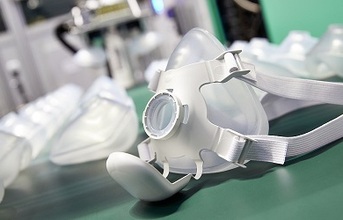
The face mask consists of a soft LSR mask and a firm PP shield with eyelets for fastening the elastic straps. For everyday use, the opening can be closed by a so-called flow gate.
After Arburg started producing protective glasses on Allrounder injection moulding machines at its headquarters in Lossburg (Germany) in mid-April, the mechanical engineering company has now launched an additional project to combat the spread of the coronavirus: Since 11 May, face masks are injection moulded from LSR (liquid silicone rubber) and PP (polypropylene). About 3,500 of these multifunctional high-tech masks are expected to be produced daily under series production conditions. The product will initially be used to protect the company's own employees worldwide and will then be distributed as quickly as possible via the district of Freudenstadt to hospitals and care facilities.
"We are involved in various aid initiatives and are also push internal company projects such as this face mask. The demand is enormous. We are receiving specific requests from hospitals and nursing homes from all over the region," says Gerhard Böhm, Arburg Managing Director Sales, regarding the current situation. "We developed the high-quality and sustainable masks made of flexible LSR and PP ourselves and additively manufactured the first prototypes with our Freeformers. The LSR component and mould simulation was carried out using the Sigmasoft software from Sigma Engineering. In a record time of only around five weeks, our partners Polar-Form and Foboha built the corresponding injection moulds for the LSR and PP components. This means that we can now start series production in Lossburg." The companies Ewikon (cold runner) and Männer (hot runner) were also involved in the implementation of the mould technology. Other partners were Barth Mechanik (gripper) and Packmat (packaging technology), the raw material for several 10,000 masks was sponsored by the chemical group Wacker and Borealis.
END