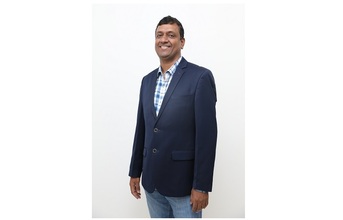
Congratulations on establishing the Additive Manufacturing Center in Bengaluru recently. How important is this initiative from the perspective of developing the additive manufacturing ecosystem in India?
The world is witnessing a rising demand for digital manufacturing and 3D printing is enabling this journey across several industries such as transportation, industrial, medical and consumer products. Additive Manufacturing (AM) ecosystem is growing at a rapid pace in Asia pacific as well as India markets to cater the needs of the industry. The Wabtec Additive Manufacturing Center is another step in our Industry 4.0 journey as we continue to integrate smart digital technologies and production systems to drive innovation and deliver cutting-edge solutions to our customers. Our India Additive manufacturing center is also a Center of Excellence (C0E) in MJF (Multi Jet Fusion) technology for the Global Wabtec Corporation. This CoE in the India will enable faster adoption of AM technology and this center opens up this expertise to be leveraged by the Indian AM community and users. This is a significant initiative for Indian AM ecosystem and the partnerships that enable more offerings in terms of better AM technology, materials and bring in design expertise to cater to the 3D printing services requirements of the Indian industry. Bangalore is also one of the regions, which houses many 3D printers because of its proximity to key aerospace sectors and many multi-national design companies in the IT corridor. We are proud to say that we are one of the first to adapt the MJF 3D printing technology commercially in India.
How would you analyse the evolution of additive manufacturing as a technology both in India as well as globally?
Industry 4.0 is the new disruptor in the world of manufacturing globally and now in India. We are in a digital age and the digital manufacturing is being adapted worldwide. This is transforming the supply chain. AM technology brings in lot of advantages, in terms of part consolidation, light-weighting to mass-customization, faster Go-To-Market cycle time for new designs and a digital inventory. This is also being proven to be a more sustainable manufacturing technology. However, there is also a greater need to accelerate this adoption in regions, like India, which is line with the Industry 4.0 journey.
While AM or 3D-printing technology was originally introduced to support faster prototyping and cycle time reduction, the technology and associated solutions have evolved in last few years at rapid pace. Current technology allows us to deliver speed and high quality at lower cost. However, this requires expertise to identify the opportunity, right printing technology, printing machine and the materials used. Wabtec has invested in these areas over many years and gained tremendous expertise. This investment enabled the company to establish this Global CoE. Wabtec is extending this capability to other industries in a true ‘atmanirbhar' (self-reliant) approach.
While additive manufacturing is a very generic term, there are many types of this technology. What will be the focus at your Additive Manufacturing Center?
There are many technologies that are proven, and some are still evolving. We are starting our journey with consulting in MJF (multi jet fusion), DMLM (direct metal laser melting), FDM (Fused deposition model), SLA (stereolithography) and Binder jet technologies and manufacturing services, and MJF technology as far as manufacturing services are concerned. These are also AM technologies that we have adopted internally and gained significant experience over many years.
Which are the different materials that this Additive Manufacturing Center can use successfully?
We have successfully used both metal alloys from Stainless Steel to aerospace-grade Nickle- chromium alloys (IN718) and in polymers, such as polyamide composites family, and high strength polymers such as PEEK (Polyether ether ketone), PEKK (Polyetherketoneketone), etc. We are now exploring more options such as, TPU, TPA and PP to add to our material suite.
Bengaluru is India's aerospace manufacturing hub. Since aerospace manufacturing has started adopting additive manufacturing to a large extent, will you also be looking at reaching out to the players in this segment?
AM technology is a digital technology and is industry agnostic. This technology can be adapted to all industry segments and many such examples are available. We will be open to serving customers in all segments.
Which are the other key industry sectors that this Center will be catering to?
We are currently focusing on railroad industry and service industries.
I understand that MSMEs will be a major focus area for this Center. How will you be addressing the needs of the Indian MSMEs?
We are opening the unique offerings of the Center to the Indian MSMEs. The speed AM provides a key factor in addressing MSMEs' needs.
Additive manufacturing is constantly evolving as a technology with regards to the processes, systems as well as materials. How will this Additive Manufacturing Center contribute to the ongoing research and development?
The AM technology is in different stages of evolution. Wabtec is gaining the expertise needed to adapt to this technology. R&D is essential to understanding material characteristics and how the product behaves in real-life field conditions in terms of temperature, vibrations and fatigue. Wabtec has a significant testing infrastructure for product qualification, which is complemented by a R&D ecosystem in Bangalore. Railroad companies operate differently in terms of product life performance ranging from five to 15 years and some of the systems run more than 20 years. That's where more of the R&D efforts are going. The AM center will enable more and faster product exploration using additive technology. Wabtec also is focusing on the production processes and many post-processing techniques, for AM at the center.
END