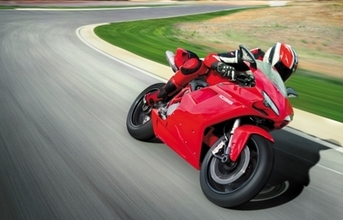
Ducati has realised that the machining of valuable components for its Desmodromic engines must be carefully controlled. Different tools are used hundreds of thousands of times during the course of a year, with the constant risk of a chipped or broken tool being picked up from the magazine, which would result in serious problems. This has been solved using a Renishaw tool breakage detection system based on innovative non-contact laser technology.
The most important stage of the Ducati Desmodromic camshaft production process is carried out on two Stama machining centres. The machines work non-stop throughout the year producing camshafts for all the different Ducati engines.
Fulvio Abbondi, Manufacturing Technology Specialist at Ducati Motor, comments, "Great precision is required when making the shaft, with the rather elaborate machining process carried out entirely within our factory. This is a very expensive component. It is made of a special steel alloy and is already expensive when, as a blank, it reaches the machine tool, after its first rough-turning".
A tool breakage during the camshaft production process would be particularly serious, and could result in scrap, costly re-machining and wasted time. There could also be damage to the machine spindle which, when added to the cost of the specialist tools themselves, would total thousands of Euro.
Taking control
Abbondi mentions the role played by tool breakage detection. "It is essential that checks be carried out on the work performed by the machines. Renishaw NC4 systems were installed on two work centres: immediately after a tool is loaded in the spindle ready for machining, it crosses the device's beam at a set height. If the cutting tip is broken, for example instead of being 100mm long it is 97mm, the laser system triggers an alarm. Clearly, each tool has its own length, diameter, etc. and the system takes this into account when the tool passes through the checking beam."