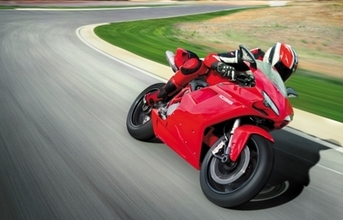
Checking with light
Improvements in laser technology have led to the development of non-contact detection systems, capable of safely measuring ever smaller tools. A laser beam runs between a transmitter and a receiver, fitted on the machine table or mounted on opposite sides of it, so that the beam crosses the operating area. When the tool enters the beam, the amount of light detected by the receiver is reduced, which generates a trigger pulse. If no reduction in light is detected, the system emits a tool-broken signal.
The Desmodromic system
The vast majority of the world's motor manufacturers use return springs in their engines to close the (exhaust and inlet) valves, these springs pulling the valve back to its original position after operation. The one exception to this is Ducati, achieving great advantages with a less conventional Desmodromic system. Desmodromic distribution offers greater engine reliability at high speeds, by solving the problem of spring inertia and reducing operating friction by about 30 percent. In theory the engine can easily top 20,000 RPM.
Desmodromic uses a mechanical system to close the valves, a concept originated in America but then abandoned due to excessive cost. Bologna's famous manufacturer had other ideas however, incorporating desmodromic distribution into its two-cylinder engines in 1972, and using this winning feature for decades. The valves are closed by a special cam rather than a simple spring, in every respect creating a strict link between the valve and its position - the term desmodromic originates from the Greek ‘desmòs', meaning ‘link'.
The Desmodromic system introduces major complications to the design and manufacture of components such as camshafts. The cam itself is not a simple conventional cam shape, instead using special lifting ramps. Ducati's design team has carefully designed the shape so as to achieve the required acceleration and speed performance. Precision is everything; the "clearance" between the stem and the cam is adjusted by hand during assembly and is a critical operation. As Abbondi says, "It's not possible to take up the slack as you can with hydraulic tappets on cars. We use one pad at the bottom and one at the top and these must be adjusted with extreme precision."
Source: Renishaw
END