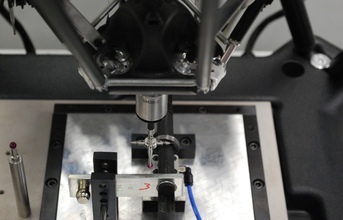
Eponsa, a manufacturer of automotive components located near Barcelona, Spain, has purchased a versatile and innovative shop-floor comparative gauge, the new Renishaw Equator. The purpose is to check the quality of stamped parts and assemblies. This will reduce non-productive waiting times to a fraction of the time taken now, while maintaining the high quality and manufacturing efficiencies that are critical for the success of an automotive subcontractor. Other advantages for Eponsa are that Equator can scan the form of part features with its SP25 probe and change styli with the stylus change rack, included as standard, to check a large variety of parts.
Eponsa believes "Equator could reduce or eliminate quality room waiting times. This is because Equator can be used on the shop floor, alongside the machines producing the parts, and with the low purchase cost we can have several Equators positioned where we need them. We plan to have Equators alongside the stamping area and in the area for assembling mechanisms, where they will be particularly important. The speed of operation and measurement capability of Equator will ensure rapid, comprehensive and fully automated gauging."
Automated shop-floor gauging
Eponsa believes that Equator will be welcomed on the shop floor since it will reduce the workload considerably. Eponsa operators are inspecting thousands of parts every day, using documented procedures. Visual checks are done to ensure holes are present and that there are no cracks in the material, followed by dimensional measurements with hand instruments like callipers and plug gauges. Because the stamping processes are automated, making them very consistent and reducing the chances of human error, operators can usually detect potential problems before scrap parts are made, to ensure 100 percent good parts.
However measurement with hand gauges is time consuming, repetitive and all down to the skill of the operator - there is more chance of the inspection process being wrong than the manufacturing process. Equator's repeatability is set to change all that.