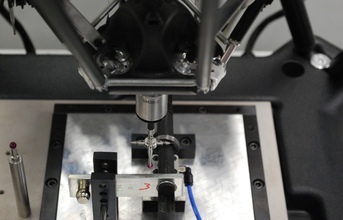
Equator is an independent and traceable test of part quality, with the difference that all the operators can use it rather than just quality staff - currently a quality inspector walks around the plant constantly checking that procedures are being followed and parts are good. This is done with a visual check followed by taking the last part in every batch and performing a full inspection in the quality room. Experience has shown that if the last part is good then the whole batch is good, but this still means a long queue at the quality room.
Easy shop floor use
The Equator system includes easy to use graphical software called MODUS Organiser, which is designed for shop floor operators to activate checks, with just a few minutes of training. This software is vital to the operation of Equator, "MODUS Organiser is the perfect way to run Equator on the shop floor, it is so simple and useful. The operators are able to choose programs and start checking the parts in a few seconds, with an immediate view of how long the check will take on a countdown timer. Once the check is complete the operator sees a clear indication of whether a part has passed or failed - in the quality department we then only have to deal with any suspicious parts, instead of every part. This is reducing the load on the quality department considerably."
Restricted access to programs
The gauging programs are written using Renishaw MODUS software, but use of this is access-controlled. As Eponsa says "It is a very good idea that only programmers can create and change programs, we can then set up the Equators knowing that the programs are running correctly and operators will not be making any changes. We make it easy for the operators to find the right program in MODUS Organiser by including photos of the part, which also shows them how the part is placed on the fixture. The intention is to use as few fixtures as possible, with many parts using each configuration."
Gauging repeatability through mastering
Equator uses a comparison method of mastering and measuring that will be very familiar to any existing users of dedicated gauging systems. A master component with features of known dimensions is used to ‘zero' the system, with all subsequent measurements compared to this part. The key to the Equator system is a highly repeatable and radically different metrology mechanism based on a structure known as parallel kinematics. This mechanism is lightweight, allowing rapid motion, yet very stiff during comparison measurement of features, with repeatability of less than ±2 µm. This has been proven on a wide variety of both prismatic and free-form features.
Manufacturing at Eponsa
Eighty percent of Eponsa's business is producing automotive components, the other 20 percent is general subcontract stamping, welding and assembly work. Designing and commissioning all their quality and manufacturing processes themselves is a big advantage, allowing them total control. This includes design of the stamping tools and welding/assembly jigs.
Eponsa is certified to ISO-TS16949, a specific standard for the automotive industry and ISO14001. It directly supplies factories around the world in Mexico, South Africa, Germany, Hungary, China and Korea.
Improve efficiency and reduce costs
The pressure on automotive subcontractors to reduce costs while simultaneously improving efficiency and quality might seem to be at odds with each other, but Eponsa firmly believe that Equator technology is the break-through they need to help them achieve this.
Courtesy: Renishaw
END