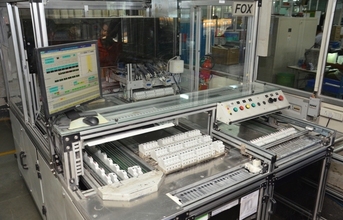
Kantoor of P+F India rightly says that the goal of today's manufacturing processes is to reduce waste in human effort, inventory and time to become highly responsive to customers' demands while producing world class quality in most efficient and economical manner. "Introduction of automation reduces over-production, waiting time, transportation, inventory, inappropriate processing, excess motion and product defects."
Chawla of Legrand India says that automated systems are always aligned to manufacturing principles to make them viable and efficient. "Bottlenecks in operations are identified and automated to ensure single piece flow which is a prerequisite for lean manufacturing. This helps in bringing flexibility of manufacturing operations provided the set up time or change over time can be minimised."
Impact on safety and machine performance Legrand India's Chawla believes that industrial automation improves machine safety as it reduces manual interventions to a great extent. "Sensors are installed in order to stop the machine abruptly to avoid any accidents. Also sometimes human speed can't match machine speed (For example, robotic arm on Injection machine). Hence in these operations, it is important to have automated systems to improve machine performance and quality. To monitor the machine performance we have OEE indicator. Effort is continuously exerted to improve upon the key factors."
According to Milind Kulkarni, Head Business Development, Factory Automation, Siemens India, industrial automation provides the required degree of accuracy and repeatability of performance for machines. "Additionally, it increases throughput of the machines without compromising on safety of overall operations. This safeguards not only machines but the machine operators as well. Safety norms need to be analysed critically to determine the type and level of Automation (SIL level) that needs to be employed in the machine." When it comes to machine safety and performance, automated manufacturing process has its own competitive edge and advantages, according to the Shakti Pumps CMD. "Since automated system performs the actions in a specific and cyclic pattern, it is easy to forecast the maintenance and safety requirements. As far as the safety of workers is concerned, automated system needs special safety set up to ensure that unwanted human interference, presence is avoided," he says.
Rajkumar of Grundfos gives an example: "The PLC programming in the machineries helps us find out the malfunction of the system and this is communicated online. This results in a quick reset to its original program and the equipment start operating correctly, thereby reducing the down time and manual intervention. The fail and safe mode programs helps stop the line if anything goes wrong and allows us to analyse the errors and rectify it quickly. This avoids the accidents in the line and damage of the equipment."
Sydney Quadros, AGM - Offer Marketing (Industry OEM Business), Schneider Electric India, says that in recent years, the concept of functional safety has emerged: it refers to the overall safety of the Equipment Under Control (EUC) and the EUC control system. "Functional safety depends on the correct functioning or operation of the electrical/electronic/programmable electronic systems and other technology safety-related systems, as well as on external risk reduction facilities. The term correct functioning means that operation is correct, not merely what is expected. Therefore appropriate selection of the functions is essential. In the past, designers tended to choose components in the highest-level category of EN 954-1, instead of choosing components in a lower category which might actually offer more suitable functions. The new EN ISO 13849-1 and EN 62061 standards help address the weaknesses of EN 954-1. Although they still require consideration of circuit architecture as in EN 954-1, they also take into account the reliability of the safety circuit components and the circuit's ability to detect/diagnose faults as well as the probability of common cause failure."
P+F India's Kantoor strongly believes that industrial automation improves workplace safety and protects workers from injury. Automated systems can work in environments which are considered hazardous for human beings. Also in areas where the human intervention is must automation can be used to provide safety to workers by the use of safety certified equipments related to plant and machine safety like safety sensors, safety light curtains, perimeter guards, interlock switches, process sensors, PLCs etc.