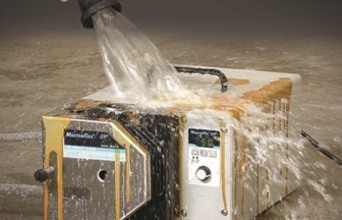
Handling viscous materials
A manufacturer needs to pump 100 percent glycerol from a 55-gallon drum into six smaller containers. Once these six containers are filled with glycerol, the chemical is used to lubricate needles for the manufacturer's process.
A solenoid diaphragm pump may seem like a valid choice as a typical metering pump, but it does not work well with high viscosities. The flow of this pump would be significantly reduced due to the 1400-cp viscosity of glycerol. The solenoid diaphragm pump is also difficult to clean and has numerous replacement parts including diaphragms and internal valves. Finally, the check valves may stick, rendering the pump inoperable.
Instead, the peristaltic pump handles high viscosities well and would improve the manufacturer's flow rate. Because the fluid in a peristaltic pump does not come in contact with internal pump parts—it only contacts the tubing—the pump remains clean and free of residue. Tubing is easily replaced, reducing overall maintenance time, and the pump has excellent self-priming capabilities.
Handling aggressive chemical and solvents
A rubber manufacturer needs to dispense one-ml doses of methyl ethyl ketone (MEK) as a primer in the first step of the vulcanisation process (treating rubber to give it certain properties). The manufacturer needs a pump that is easy to operate.
The tendency may be to get a piston pump for its relative accuracy when pumping small volumes. In this case, though, a piston pump makes it difficult to regulate the one-ml doses. The chemical compatibility of the internal parts in the piston pump is challenging and the pump head and valves are hard to clean. Finally, the piston pump can't run dry. A peristaltic pump would be a better choice. Its controls are simple to operate, satisfying one of the key requirements of the manufacturer. Tubing formulations are available that are chemically compatible with MEK. The tubing is easy to change and cleaning the pump is also simple, reducing labour for operators. The pump has no service kits or valves to maintain. Peristaltic pumps can run dry to prime.