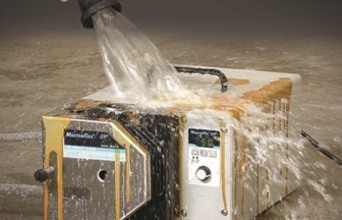
In real-world conditions, pumps can be challenging. Some do not handle particulates, some are difficult to use with high-viscosity materials, others have valves that stick and seals that fail—all common complaints for everyday pump users. Others have maintenance issues such as cleaning and replacing parts that result in costly downtime.
While one solution may not fit all pump applications, comparing the type of pump in use to a peristaltic pump is a good place to start. A peristaltic pump works by an alternating pattern of squeezing and releasing flexible tubing to move fluid through the pump. As a roller passes over the tubing, it is first occluded (squeezed), then released.
The progression of this squeezed area forces fluid to move in front of the roller. The tubing behind the rollers recovers its shape, creates a vacuum, and draws fluid in behind it. As the roller moves faster, vacuum pockets are created more quickly and the fluid moving through the system picks up speed. The rollers act as check valves to prevent siphoning or loss of prime. Let's look at some application examples that illustrate some specific advantages of peristaltic pumps.
Chemical processing applications
International company HEL specialises in process safety and development and provides pre-pilot scale chemical reactors and systems to the pharmaceutical, fine chemical, petrochemical industries, and academia.
HEL's project team prepared three automated reactor systems for a process chemistry application in which their client required phase separation. The client needed an automated system and HEL project leaders turned to Cole-Parmer for help in outfitting the system with the correct pumping technology.
Chemical reactor systems require a pump system that can deliver an accurate volume of fluid while maintaining purity. Cole-Parmer recommended its peristaltic pump for this application as it offers high accuracy. Additionally, the only wetted part is the pump's tubing, ensuring high purity.
What a peristaltic pump can do? Particulate handling: Peristaltic pumps can handle undissolved solids and dirty fluids containing particulates. For manufacturing and industrial applications, they can pump wastewater, suspended solids, harsh chemicals, and more. High viscosities: The design of peristaltic pumps makes them suitable for abrasive and/or viscous fluids such as lubricants, slurries, paints, liquid waste, and more. Maintenance of sterility: Because the fluid that is pumped does not come in contact with the internal pump parts, the fluid is not contaminated and the parts remain clog-free. Simply using sterilised tubing and other fluid path components will maintain fluid sterility. Chemical compatibility: The composition of the tubing used in the pump is the key factor in chemical compatibility. Hundreds of tubing options are available and free databases (such as ColeParmer.com/Chemical-Resistance) allow users to compare tubing materials to assess their compatibility with a chosen chemical. Ability to run dry: Pumps gases, liquids, or mixed phases without damaging the pump. Ease of use: Most peristaltic pumps can be installed within minutes. Their interfaces are easy to use and those with digital displays can be read from across an average-sized room. Some have reversible motors to purge tubing and some have remote control capabilities. Reduced maintenance: With no seals, valves, or glands, these pumps are easier to maintain. Tubing is easy to replace with few or no tools needed; simply switch the old tubing with new tubing. Some tubing is formulated for longer life, which further reduces costs. Actual tubing life depends on pump speed and pressure, tubing material, chemical compatibility, and the abrasiveness of the media being pumped. |