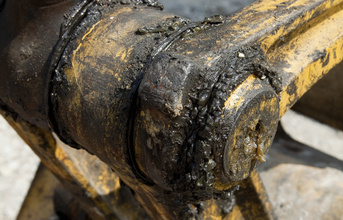
Heavy-duty applications for plain bearings, generally seen in construction machines, agricultural equipment, hydraulic cylinders, mounting brackets, etc., have very challenging technical requirements considering the harsh and dirty environments these machines are used in. Generally, metallic bearings used in such applications are heavily greased. Adverse weather conditions can lead bearings to corrosion and premature failure in case of missing lubrication or insufficient lubrication.
The motion plastic solution provider igus offers multiple polymer plain bearings as an alternative to frequently used lubricated metal bearings. The range of heavy-duty polymer bearing from igus includes:
1. Injection moulded plain polymer bearings from materials like Iglidur Q, Iglidur Q2, Iglidur Q2E, Iglidur Z, Iglidur G etc. These materials can offer long service life at high loads with extreme conditions. For example, a material like Iglidur Q2 offers a high wear resistance with a maximum permissible compressive strength of up to 130 Mpa.
2. Fibre wound plain polymer bearings from materials like Iglidur TX1 and Iglidur TX2. These bearings are made of high-strength filament fabric. The extremely strong filaments in its specially interwoven design ensure maximum wear resistance and a maximum permissible compressive strength of up to 400 MPa.
All iglidur plain bearings, including materials mentioned above, are self-lubricating and operate in dry condition. This prevents dirt from adhering to the bearing points. It reduces maintenance and repair costs and machine failures due to insufficient lubrication. With Iglidur bearings, customers not only save on the cost of lubrication oil (or grease) and maintenance time but also release no lubricant in the environment. This accounts for increased sustainability requirements. A 16-tonne excavator needs between 50 to 60 litres of lubricants per year, ending up in the soil. With Iglidur bearings in use, contamination of soil can be reduced.
Iglidur polymer materials are extensively tested on the indoor and outdoor test rigs in the 3,800 square metres igus test laboratory. Pivot tests at 30 Mpa pressure and a pivoting angle of 30 degrees were carried out for 200,000 cycles on multiple Iglidur materials with various shaft combinations. It showed wear results of as small as 0.05 mm in some heavy-duty materials in combination with GKF shafts. GKF treatment is a surface technology solution from igus that protects shafts from corrosion and wear. In this process, the shafts are gas nitride, and their tribological properties are optimised in additional processes.