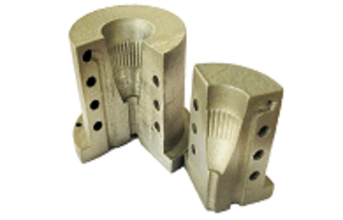
How would you analyse the evolution of additive manufacturing both in India as well as globally?
The manufacturing industry is presently found to be in the middle of a technological renaissance, and is expected to embrace technological advancements to enhance productivity and gain competitive advantage. Additive manufacturing technology is evolving rapidly. Additive manufacturing has come a long way in the past couple of decades, especially in the last five years to evolve into a viable industrial manufacturing solution. The technology continues to evolve from the initial days where applications were restricted to simple rapid prototyping are now being used for batch production of parts and even large scale production of end-use parts for various industrial applications. Materials in additive manufacturing are defined by the technology. From polymers to metals and exotic materials such as Kevlar, graphite, diamond and even human tissues, this partnership between the material and technology is only going to get stronger as more material chemistry is being explored. 3D printing is often referred to as "rapid prototyping"; however, it may take several hours to print a part on a single laser machine. However, that day is not far when 3D printer manufacturers come up with multi-laser machines (up to 12 lasers!!) having larger work envelopes that offer higher productivity, where multiple parts can be printed simultaneously. India is yet to see large scale adoption of this technology. The low cost of labour and engineering are an inhibitor to proliferation of this technology in the Indian market. Though the first metal 3D printing machine arrived over 15 years ago, additive manufacturing technology is concentrated in Government research organisations for defence or aerospace applications or Government institutes for specialised applications. It is only in the past five years, that the industry is preparing to invest in the additive manufacturing technology and identifying applications by leveraging on the advantages of this technology.
While additive manufacturing is a very generic term, there are many types of this technology. Tell us more about the different types of this technology?
In additive manufacturing, one creates a design of an object using software, and the 3D printer forms the object by adding materials layer upon layer until the final shape of the object is realised. The object can be made using a number of printable materials.
Fused Deposition Modelling (FDM), also referred to as Fused Filament Fabrication (FFF) is a material extrusion process where a spool of solid plastic material is pushed through a heated nozzle. The printer deposits the melted plastic filament on a build platform along a predetermined path. Up on cooling the filament takes the shape of solid object. The most common materials that can be printed are PLA, ABS, PET, PETG and TPU. Stereolithography or SLA, world's first 3D printing technology was invented by Chuck Hull in 1986, who filed a patent on the technology. It works on a 3D printing concept called Vat Polymerization where a vat of photopolymer resin is selectively cured by a solid-state laser, building it up layer by layer.
Selective Laser Sintering (SLS) is creating an object using the concept of Powder Bed Fusion technology and polymer powder. A bin of thermoplastic powder is heated to just below its melting point. Then, a recoater deposits a thin layer of the powder onto the build platform. A laser beam scans the surface where it selectively "sinters" or solidifies the powder. This step is repeated until all objects are manufactured. The powder that is not sintered supports the object that has been sintered, eliminating the need for support structures.
Material Jetting (MJ) as process goes by the same name and works similar to the common inkjet printer. However, instead of printing a single layer of ink, multiple layers are built upon each other to create a solid object. Ultra violet light cures/solidifies the droplets of photopolymer that is jetted by the print head. The build platform lowers by one layer, once a layer is deposited and cured and the process is repeated until the 3D object is formed.
Binder Jetting (BJ) is a similar to SLS technology, here regions of powder are selectively bind by a liquid bonding agent. However, in binder jetting unlike the SLS, the print head travels over the powder surface depositing binder droplets. This process can be used to make parts from metals as well as sand.
Direct Metal Laser Sintering (DMLS) and Selective Laser Melting (SLM) is based on the concept of powder bed fusion technology and produces parts which from a process perspective is very similar to SLS. This technology is deployed to produce metal parts. While, the metal powder is not melted in DMLS, but instead heats up to a point so that it would be sintered on a molecular level, SLM uses the laser to fully melt of the metal powder, thereby forming a homogeneous part. The major difference between DMLS and SLM is that the former produces parts from metal alloys, while the latter form parts from single element materials. Both the processes require structural supports to support the printed parts. To relieve the parts from internal stresses, the printed parts are later subjected to heat treatment process.
Which are the ideal applications of additive manufacturing?
From prototyping to tooling to end use part manufacturing for sectors such as medical, dental, aerospace & defence, automotive and jewellery, new and innovative applications of additive manufacturing are currently being explored. The aerospace industry was one of the first adopters of additive manufacturing as this has helped improve the part performance and aided weight reduction. Automotive industry is a high-volume production industry with over 1,00,000 parts per year. Additive Manufacturing here has predominantly been used for prototyping rather than manufacturing of end use parts. There are many applications have been happening for some time now with 3D printing of aircraft parts to make lighter and more efficient engines and 3D printed turbine components. One of the biggest users of 3D printing is the dental industry. Scans are taken from the patient's mouth to 3D print customised dental copings to fix dental problems. With additive manufacturing, patient specific implants can be printed with minimum lead times. Additive manufacturing also offers the ability to print lattice patterns on the surface of implants. These lattice patterns aid osseointegration. Additive manufacturing seems to be a game changing technology when it comes to complex tooling. Conformal cooling is possible using additive manufacturing, where metal powder is melted selectively by laser beam. This has helped increase the productivity of injection moulding and contributed to better quality of plastic parts.
What are the key advantages of additive manufacturing vis-à-vis traditional manufacturing?
The benefits Additive manufacturing has got to offer over traditional manufacturing are plenty. With additive manufacturing, an organisation can reap the following benefits:
Topology optimisation: It is optimising the object structure through weight reduction and generative design concepts without deteriorating the quality or strength of object. The parts become light weight and stronger and display enhanced mechanical properties.
Freedom to design: Through Additive Manufacturing, intricate and complex geometry parts can be printed without any hindrance. It gives the designer freedom to explore designing bionic structures to bring about weight reduction in parts.
Rapid prototyping: The product development cycles are drastically reduced in additive manufacturing. Through generative designing there is a flexibility of creating, testing & validating multiple product design iterations to suit the end application or customer's preferences.
On-demand manufacturing: There is the flexibility to print parts only when it is needed. This brings down the unnecessary inventory carrying costs. This is extremely useful for spare parts management and organisations can enjoy reduced costs on inventory, supply chains and spares manufacturing.
Briefly share some information about the most interesting project undertaken by your organisation in the recent times.
It has been an exciting journey so far. There have been some very interesting projects that we have executed. It is a proud moment for us to be associated with ISRO for 3D printing The National Emblem of India for the Chandrayaan II mission. The national emblem was to be fixed to one of the rear wheels of "Pragyaan", the rover. It was proposed that as the rover moved on the surface of the moon, it would leave an impression of the national emblem on the moon. We had also 3D printed rear wheel hubs for an EV racing event. This was an interesting one as we had to redesign the wheel hubs completely. The wheel hubs were topologically optimised and lattice structures were incorporated to make the parts light weight without compromising on the functionality. Very recently, during the initial phases of lockdown when the country was shut, we printed crucial ventilator parts that were utilised by a company which is currently working on developing and manufacturing indigenous ventilators. These ventilators parts were developed, printed and dispatched in less than 24 hours from the enquiry!! Then there is of course the die mould industry, where we have been doing a lot of printing. The Indian tool manufacturers are gradually beginning realise the advantages offered by the concept of conformal cooling.
Aerospace manufacturing uses a variety of materials like steel, aluminium, titanium as well as different plastics. How is additive manufacturing addressing this material complexity?
Today, it's additive manufacturing that has opened up new avenues for design and manufacturing in the aerospace manufacturing segment. For the aerospace industry, also known as the largest consumer titanium, weight reduction is a major issue for the aerospace industry. Titanium is and expensive metal and when you produce complex parts by machining away material from a solid block, major chunk of the metal you had paid is going away as scrap. There is a costly imbalance between the metal in the final component and the weight of the metal you had purchased. Additive Manufacturing through design and geometrical freedom facilitates a Buy-to-Fly ratio closer to one. During these challenging times of increasing fuel costs and fragile economic conditions, and with the commercial aviation industry operating on wafer thin profit margins, improving fuel efficiency of engines is key. Materials in additive manufacturing are defined by the technology. This partnership between the material and technology is only going to get stronger as more materials are being explored. There is an interesting case of GE aviation where they have 3D printed fuel nozzles that have been tested for airworthiness. Approximately, 50,000 of these are currently inside the jet engines and flying. The Boeing 777x aircraft that had successfully completed the maiden test flight in January 2020 had over 300 additively manufactured parts in the GE powered engine.
How can one be sure of the structural integrity of a metal component made using additive manufacturing? Also, is it true that many components (made with additive manufacturing) require post-process machining? How does this impact the manufacturing process from the cost and time perspective?
The printed parts are subjected to a thorough and rigorous testing. The process itself takes care of structural integrity in AM. Additively manufactured parts are better than casting; it is just a process of micro-welding, where the present layer that is being melted layer fuses with the previous layer. Research has shown it to have properties similar to forged parts. Almost all metal parts need to be post processed to finish it to the desired size or surface finish. For parts with open tolerances direct applications is suitable. Otherwise, additive manufacturing replaces raw material sourcing (Casting, forging, extrusion, solid block, etc.), rough machining, and semi-finishing. Only final finishing process may be required for the parts suiting the applications. Considering the time required for all the above processes put together, additive manufacturing is faster. If the material that has to be removed is higher as in the case of aerospace components where input is mostly solid blocks of metal, then additive manufacturing is more suitable. Also, when the complexity of the part is higher requiring multiple machining setups or multi-part assembly additive manufacturing offers a better solution.
How has the corona virus outbreak affected your businesses? In what way and how are you dealing with the same?
The outbreak did not change much for our business. Many of the customers who had an R&D budget to get parts done have decided to postpone investments especially in the automotive sector. Many others affected by supply chain issues are taking the printing route to source parts faster. Many ventilator parts are being printed today. AM will get more prominence considering its speed to produce parts during the development stage. Currently the focus is to bring more awareness in diverse sectors. They say, when one door closes, may others open. It's about finding the right opportunity in the right market with the right customers.
END