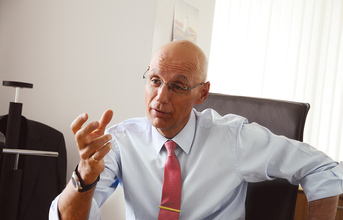
It is not surprising that he has focused on all these three aspects at the Volkswagen Chakan plant in Pune. "India is a very complex and diverse country and it is not possible to import or enforce any outside culture on this society. So we are looking to combine the best of Indian and German culture at our factory. We are working towards it and making improvements."
He then explains the importance of discipline in the context of the plant. The Chakan plant uses about 35 percent automation. The rest is obviously done manually. "Combining and coordinating the automated process with the manual process requires lots of discipline. And that's why training is a vital aspect of our plant culture. We are continuously communicating with our people on this aspect," Lauenroth says.
Under Lauenroth's leadership, the Volkswagen Chakan plant is focused on standardisation of the processes. This is achieved both manually as well as through automation. For example, Volkswagen is the only Indian manufacturer using the Laser Roof Welding technology, which is one of the core strengths of Volkswagen. "With our constant training, the employees in the shop floors are able to produce highest quality consistently," he says.
The plant follows Kontinuierlicher Verbesserungsprozess or KVP as the standard working procedure. KVP simple means Continuous improvement process. "KVP aims towards optimum utilisation of available resources - both in terms of manual as well as the machinery. To make our people inculcate this system, we have been regularly conducting KVP workshops. Last year we did 72 workshops and this year we will be doing 67 workshops. This has helped us cut down cost at the manufacturing level to a great extent."
Even in terms of the plant layout, Volkswagen follows standardisation across the world. "The Chakan Plant layout is also planned to optimise logistics and the overall flow of work. We established this Plant with a long term perspective. Automation, wherever implemented, was done in a way that it could be adapted to the changes and improvements done in manufacturing over a period of time. Also, we are using the same robots for manufacturing different products. For example the ‘Konzern Framer' enables us to build up to four different types of bodies on the same line through automation," he explains.
The next level - Mach 18. Factory
The Volkswagen Group is implementing a strategic initiative aimed at achieving a comprehensive optimisation both in ecological as well as economical aspects. This initiative is based on six pillars: Productivity, Quality, Innovation, Team Culture, Expertise and Ramp Ups. For example, innovation is driven by the need to come with new ideas, sharing of those ideas and effective implementation of the same. "We plan to have at least 30 robust innovation ideas by 2018," shares Lauenroth. |