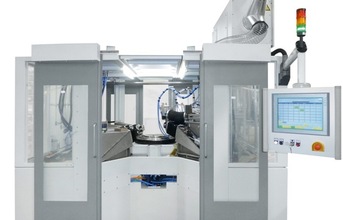
Selective process
The electro-chemical process ensures a particularly soft removal of the material. The workpiece acts as positive anode and the tool as negative cathode. Between the two flows an electrolyte solution that dissolves metal ions on the workpiece. The contour of the cathode and the workpiece with their active, current-conducting sectors, are matched, to ensure that the material removal on the workpiece leads to the desired contour of the component. Contours, channels, grooves and cavities are generated without touching the component - and at the highest possible precision. And tool wear is minimal. With PECM, Emag has developed the ECM technology further. The gap, through which the electrolyte solution flows, is particularly narrow; and the flow is optimised by a mechanical oscillation. This guarantees a particularly effective and precise removal of the material. The possibilities this technology opens up are best shown by the example of blisk productions.
For the machining of turbine blade disks the specialists from Emag have developed an ECM system equipped with 11 machining stations that carry out drilling, contouring, radius machining and polishing operations in one machine. The high-tensile Inconel material is machined at a feedrate of 5 mm per minute, without burrs or negative thermal effects. The tolerances achieved are between 0.1 and 0.3 mm. The life expectancy of ECM tools is very high, making sure that the tooling costs in production are much lower than those using cutting tools for the process.
Establishing feasibility in the lab
The experts at Emag ECM see themselves as their customers' partners in development. The centre of activities is an on-site laboratory, which offers the possibility to carry out feasibility studies and preliminary investigatioaHaHns on single- and multi-axes machines. In addition, the laboratory also offers comprehensive measuring systems (roughness, contour, coordinates).
The laboratory not only establishes the feasibility of a project, but also the cost-benefit ratio of the process with a view to the specific component and the material it is made of. This way, the customer will find out what component tolerances and cycle times he can expect to achieve.