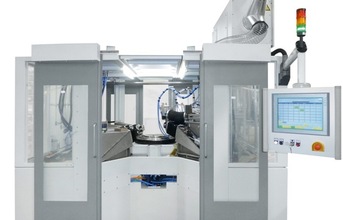
An exceptional option
Of course, this is not an unfamiliar development (growing environmental and efficiency requirements), as the automotive sector provides another example. However, in aircraft manufacture it has more extreme consequences. And the industry has arrived at a crossroads. Experts estimate that over the next two decades air traffic will increase by five percent per annum. The prediction voiced by Airbus is that there will be a demand for 7,600 new engines every ten years. Although this offers great opportunities, it is certain that to conquer new markets the aero engine manufacturers will have to come up with constantly greater improvements. New aero engines are becoming top of the agenda.
What are the manufacturing solutions that ensure the new high-performance engine components can be produced efficiently? ECM und PECM technology (Precise Electro Chemical Machining) from Emag is an exceptional option, even though many developers and design engineers have not yet recognised the fact. This process comes into its own where complex components are to be produced in demanding materials, as it machines high-tensile alloys and similar materials with a minimum of tool wear. The surfaces are of outstanding quality - with no burrs and no changes in the microstructure of the material. In contrast, using cutting processes could lead to a number of problems. The temperatures generated by traditional machining methods often have a negative effect on the microstructure of the material. Tool life in the machining of high-tensile materials is short. And the high infeed rates required to make the machining process economically viable, make the machining of filigree geometries difficult. It should therefore not come as a surprise that the demand for ECM is increasing in aero engine manufacture. Since Emag entered into this technology in 2009, a number of its machines have been delivered to the supply chain for aero engine manufacturers, where they are used to machine central components, such as blisks, disks and individual blades in nickel alloys at speed and with great precision.