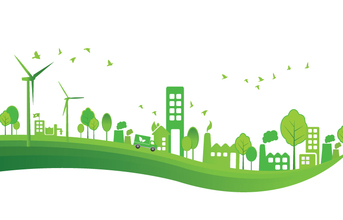
Water & energy conservationSimilarly, Henkel has deployed a rainwater harvesting project in its Thane facility. "This measure helps us save around 360,000 litre water per annum. Moreover, our manufacturing operations reduced its water consumption by 9 percent and waste generation by 17 percent at a pan India level in 2015 with respect to 2014 operations," affirmed Bandyopadhyay. HIL as well ensures that no drop of rains goes uncounted for through rain water harvesting systems. Furthermore, Dalmia Bharat has achieved positive results from various plans implemented for conserving water. "At our Dalmiapuram plant, daily water consumption was reduced by 36 percent within two years as a result of various water conservation initiatives and process modifications. The Kadapa plant in Andhra Pradesh obtained water positivity in FY 2014-15itself through rain water harvesting measures whereas at Ariyalur, we used captive power plant reject water for cement mill operations to reduce water consumption in the cement mill," remarked Tripathy.
In this comparison, Racold Thermo (P) Ltd which is taking small but important steps towards saving water. "Recycling of water through STP and ETP, timely check on plumbing fitting and fixtures to avoid any water leakages and awareness within the organisation about water crisis are some of the measure that we are taking for saving water," mentioned Mahesh Bhangale, General Manager - Manufacturing, Racold Thermo (P) Ltd. Moreover, the company is also making efforts to reduce the electricity consumption. "In our facility, we use proper ventilation to get good sunlight and air circulation.
Also, we ensure that lights are switched ON/OFF at particular time. Use of motion sensors for lights in key areas and awareness within organisation to reduce energy usage play a vital role," Bhangale continued. Besides Racold Thermo, even HIL has adopted these energy saving measures.
Identifying key areas
Making a plant energy efficient also includes the aspect of sustainable manufacturing processes. Automation plays an important role here. "Henkel Adhesives technologies' Turbhe plant reduced the batch cycle time by introducing automation thereby saving 55,440 KWH of energy," observed Bandyopadhyay.
Likewise, identifying the key areas and working towards it is secret to have clean processes. Adhering to this, Godrej Interio has identified its powder coating as one of the most energy significant processes, which draws more focus for improving energy efficiency. "We have been able to reduce energy consumption in the process through successful implementation of projects like the modulation of pumps and blowers by use of variable frequency drives, use of room temperature chemicals to eliminate the need for hot water. The project of using low bake epoxy powder helped to reduce piped natural gas (PNG) consumption," asserted Marolia.
Racold Thermo also houses similar powder coating section. "Here most of the energy is consumed in pre-treatment, preheating, powder coating and curing areas. Presently, we are using CNG gas to heat the required areas instead of consuming electricity. We have installed solar water heaters to heat the water for processing of the production. Also, we have changed over to CORONA system instead of TRIBO to avoid wastage of powder," Bhangale informed. To improve it further, the company plans to use heat pump to heat required chemicals in pretreatment areas.
(Continued on next page)