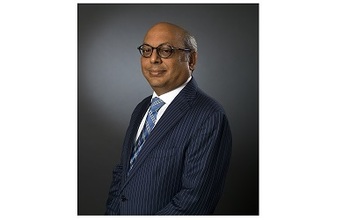
Give us an overview of the glass packaging industry in India. How's been the last one year for the industry?
The glass packaging sector in India has grown rapidly over the last two decades with significant investments in modern technology, capacity enhancement and the introduction of new products. The glass packaging market was at INR 45.5 billion during 2012-13 and is estimated to have reached INR 67.5 billion during 2017-18, with a CAGR of 8.2 percent. The glass packaging accounts for about 10 percent of India's INR 472 billion consumer packaging industry.
India is amongst the top 15 markets for glass packaging globally, however, the country's per capita consumption of container glass is low at 1.4 kg compared to other countries, exhibiting a significant opportunity for growth. Increasing health consciousness, acquisition of advanced technologies and strengthening of consumer connect will likely further drive the demand for glass packaging in the country. Adoption of latest technologies and use of automated machines in the manufacture of glass containers in the country has significantly grown in the last decade.
The glass packaging industry in India is highly fragmented with the presence of a large number of localized players and about 10 medium and large players. The top three manufacturers' together account for about 80 percent of the total installed capacity.
North India is the leading container glass market in India accounting for around 40 percent of the overall demand followed by south and west at 29 percent and 21 percent respectively. Of the total glass packaging market, food and beverages accounted for a major share of around 80 percent followed by the non-food sector at around 20 percent. The Indian container glass industry is aiming to further increase the natural gas-based operations as natural gas is clean, improves furnace performance and reduces repair and maintenance. Also, in the last twelve months, the profitability of the manufacturers who export to international markets has significantly increased as the rupee has proved to be more competitive compared to the dollar.
How's been the business for Piramal Glass and what's driving the growth?
We are the largest specialty glass player in Asia and have been the fastest growing glass company in the world during the last 15 years with a CAGR of around 15 percent. The FY '18 revenue was around $320 million with cosmetics and perfumery segment contributing around 40 percent and the rest being distributed between glass bottles for spirits and food and those for pharmaceuticals. We are offering our products in over 50 countries and over three-quarters of our revenue comes from the exports business. Today, we are the global leader in nail polish bottles, manufacturing two billion units each year that are almost half of the global demand.
It's a complex industry with fixed costs and capacities that are therefore very sensitive to variations in demand. Even the main global players in this sector have stopped growing. The key reasons for our sustained growth lie in our flexibility, our excellence in design and manufacturing, our wide global footprint, and our continuous investments in future ready and sustainable initiatives. Over the next two years, we are planning to invest over $70 million. Today we have our offices and warehousing facilities in France, Germany, USA, Brazil, India, UAE, UK, China, and Sri Lanka.
Our strong and long-term customer base is also one of the key reasons for our growth. We closely work with our customers through their product launch life-cycle to conceptualize, design, and produce a personalized glass packaging solution that exemplifies the brand value, market requirements, and product concept. Today, we have 17 of the world's top 20 cosmetic companies as our customers and most of the top global players are part of our customer list for spirits, food and pharmaceuticals segment.
What is the percentage ratio of your domestic and exports revenues?The Indian (domestic) market represents around 25 percent of our total turnover and around 75 percent is exports.
Tell us about the overall manufacturing capacities and capabilities of Piramal Glass.
We provide an integrated glass production and decoration solutions and technical expertise from concept, design, to final commercial development. We have four manufacturing facilities located in Park Hills (USA), Kosamba (India), Jambusar (India), and Horana (Sri Lanka) with an overall capacity of 1375 tonnes per day, with 12 furnaces and 55 production lines. Our glass decoration facilities are located in Kosamba (India), Horana (Sri Lanka), and Williamstown (USA).
Our facilities are supported by dedicated and modern mould design and manufacturing workshops. The mould workshops are equipped with state-of-the-art CNC machines with a separate infrastructure for the manufacturing of sample moulds. Our facilities have the latest machines and equipment sourced from globally reputed suppliers. For instance, the furnaces, distributors, and forehearths are developed by HORN and SORG (Germany); Batch House and Hot cullet conveyors are developed by Zippe (Germany); IS machines from EMHART (Switzerland) and Bottero (Italy; Stackers from Bottero (Italy); Sheppee from UK from Germany and BDF from Italy; Annealing LEHRS from Pennekamp (Germany), and Inspection Machines from EMHART (Switzerland), HEYE (Germany), IRIS (France), and TIAMA from France. We have a colouring feeder operation for the perfumery segment in technical collaboration with a world leader in colouring systems. We are the first company to offer such a solution to the customers. The colouring feeder operation helps our customers to reduce development lead time. We produce six basic colours (blue, green, purple, light grey green, dark grey, and black) in 15 different shades.
Our decoration facilities are equipped with a state of art machinery and systems. We have in-house capability for printing (ceramic, organic, and pad in one or multiple colours), coating (lacquering), hot-foil stamping, rinsing (frosting), decal, fitment/ gluing, and external metallization. We also have modern and equipped chemical laboratories in our manufacturing facilities to check, inspect, and validate all incoming raw material as well as the quality of glass on a continuous basis. Our laboratory is equipped with WDXRF S-4 for chemical composition testing of glass and raw materials; Atomic absorption spectrophotometer for metal testing at ppm level; Lambda 35 UV visible spectrophotometer, equipped with colour measurement software for colour and light transmission measurement; Petrological microscope for glass defect identification; Stereo microscope from Zeiss, Germany, for glass homogeneity testing; and Flame photometer for alkali and extract testing in glass containers.
Today, it has become very important for manufacturing organizations to be equally focused on sustainability. Tell us what is Piramal Glass is doing in this regard?
As a group, we nurture projects that are scalable and ensure to deliver a sustainable impact. As an ISO 14001 certified organization, we take responsibility for the environment around us by constantly cultivating our environmental footprint. A vital element in our environmental sustainability is to use raw material and energy responsibly. We have successfully reduced energy usage, cut carbon emissions, increased the amount of recycled glass, and created a safer and greener work environment. We have tied up with the social movement, Believers in Glass, which highlights the benefits of using glass and the health hazards pertaining to the usage of plastic. As part of our sustainability strategy, we have added a renewable power source, Solar Energy, in our consumption portfolio. We have successfully installed solar roof-top system of 2 MW at our India facility and of 3 MW at our Sri Lanka facility. We have also successfully installed Wind-Power system of 8.4 MW in India. These systems are future ready and are gaining significant popularity as a viable means to reduce carbon emissions.
Last year, Piramal Glass enhanced its ‘Cullet-Sorting' capabilities for ‘Cullet Treatment' at its Jambusar (Gujarat) facility by installing fully-automatic equipment. How has it benefitted the organization?
Yes, you are absolutely right. Last year we had enhanced our Cullet-Sorting capabilities by installing a fully-automatic high speed, optical camera based, cullet sorting equipment from Binder+Co Austria called Clarity. It ensured the cullet sourced from the open market gets completely free from any impurities and gets sorted according to colour. It had also enhanced our capability to sort glass in the smallest sizes, from 1mm onwards.
Piramal Glass has recently implemented an IoT solution on the 46 production lines across its four plants (two in India and one each in Sri Lanka and the US). What necessitated this move and how do you intend to leverage on the same?
Although we are a B2B company, we want to provide our customers, many of them millennials, a B2C experience. Real-time visibility, anytime/anywhere service, faster delivery and quality products are the benefits our customers will gain from our Digital Transformation program.
For our manufacturing operations, there has been a clear need for real-time visibility of operations to improve production efficiency and reduce defects. Glass manufacturing is a very complex process with many interacting variables.
To have a better control over our manufacturing process with actionable insights, we developed a state-of-the-art, cloud-based, IoT-enabled platform, which enables real-time monitoring of our operations. With digital technologies such as IoT and AI, we are combining science with the art of glass manufacturing to produce high-quality products.
END