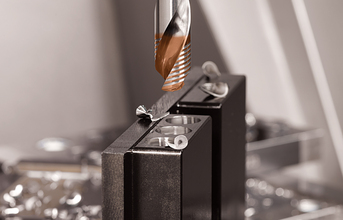
Technological progress made visible - with a new design of lands, the DC170 is unique. The copper-coloured finish with unmistakeable channel structure conceals four tangible features of a new performance class for drilling ISO-P and ISO-K materials.
As the new icon of drilling, the DC170 makes its appearance on the international stage of metal machining at the IMTEX 2015 in Bangalore. Visibly new, visibly different - a unique design of lands and copper-coloured finish symbolise a new performance class for drills.
Walter will be offering the first two models in the dimensions 16xDc and 20xDc. The newly developed DC170 offers more process reliability, stability, running smoothness and efficiency than carbide drills with traditional geometries.
More process reliability: The new drills are internally cooled. Thanks to shallow grooves, the coolant flows unimpeded, while hazardous chip jams are at the same time avoided. Because of the new design of the lands, the liquid washes around the drill continuously, producing a unique cooling effect.
Longer tool life: The solid carbide mass directly behind the cutting edge makes the DC170 incredibly sturdy. Even extreme temperatures are effectively dissipated.
Higher hole quality: An effect of the new type of alignment of the lands is significantly smoother drill running. Because they are continuously guided, vibration is reduced to a minimum, and so the DC170 wins favour across the board.
Less expensive manufacturing: The distinctive cooling channels ensure the optimum operating temperature. Drills straight from the factory are supplied with eight visible channels that can be used as a scale for regrinding.
The DC170 drills can be reconditioned up to three times, until only two cooling channels are left remaining. Users who make full use of this now-visible regrinding potential can lower their manufacturing costs.
(Continued on the next page)