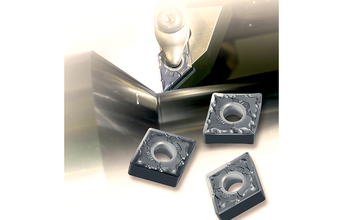
The latest MIRACLE SIGMA technology has been applied in the new (AlTi)N coated MP9005 and MP9015 series. This new Al rich, (AlTi)N coating surpasses conventional performance with a single layer that provides stabilisation of the high hardness phase to dramatically improve wear, crater and welding resistance. The grades have been developed for finish to medium turning processes and for medium to rough cutting on heat resistant alloys respectively. MP9005 is a high quality grade that surpasses the wear resistance of previous versions, making it most suitable for ISO-S05 type materials, whilst the MP9015 line is better suited to ISO-S15 materials and is highly recommended for more general purpose usage. For titanium alloys in the ISO-S15 parameters, Mitsubishi has developed its MT9015 line of uncoated cemented carbide inserts that have a sharp cutting edge but also have high fracture and wear resistance properties. This uncoated range is offered specifically for general turning of titanium alloys.
Chip Breakers
Incorporating Mitsubishi's new chipbreaker designs for the negative inserts, the R&D team has developed the LS chipbreaker for light cutting, a newly designed MS breaker for medium and general use applications and the RS breaker for rough cutting. Primarily for small depths of cut, the LS chipbreaker has enhanced chip disposal geometry for depths of cut smaller than the insert corner radius. For more general applications, the MS chipbreaker has a large two-step rake angle that enables swarf removal without tangling around the tool and workpiece when cutting at lower feeds. For more robust rough cutting, the RS chipbreaker incorporates a positive land that controls abrasion at the depth-of-cut line and eliminates chip welding that is commonplace when machining heat resistant
materials.
Easy Selection
This chipbreaker designation is simplified by Mitsubishi with its new ‘Easy Selection Breaker System' that identifies each chipbreaker by L, M and R for Light, Medium and Rough cutting with the ISO material type following. In this case, S is the ISO designation for heat resistant alloys. The formula has now been introduced to all Mitsubishi insert grades to enhance insert identification and ease of use for the end user.
All the above mentioned insert grades are available in CNMG, DNMG, SNMG, TNMG, VNMG and WNMG designations to ensure that the new grades, MP9005, MP9015 and MT9015, can improve tool life, longevity, productivity and reduce costs regardless of the turning application.
High Al and conventional coating comparison
The new technology high Al-rich (Al,Ti)N single layer coating provides stabilisation of the high hardness phase and succeeds in dramatically improving wear, crater and welding resistance.
END