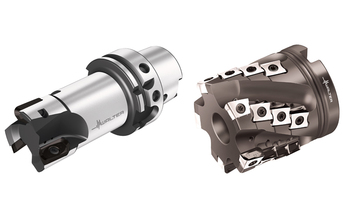
The creation of machining concepts involves tool specialists who bring their expertise in machining turning, drilling, threading or milling using a wide range of different materials. The process also involves component experts who know exactly which challenges associated with the manufacture of specific components need to be overcome.
To enable them to tailor their solutions as closely as possible to the specific requirements of the user, Walter's component managers visit their customers on a regular basis. "Our component managers are deeply involved in the topic, they speak the language of our customers and know exactly where the problem areas lie," explains Thomas Schaarschmidt. Their task is to keep up to date with what the users of Walter tools are currently doing and what optimisation measures or open topics they are looking at. Of course, they also gather feedback on the machining solutions recommended by Walter. "Generally speaking, there are one or two large manufacturers for every component - the market leaders, if you will. We use our component approach to work very closely with these companies - with great success."
Solutions with a competitive advantage
The solutions that Schaarschmidt's team develops with customers are extremely detailed, with the purpose of creating competitive advantages for customers. It is therefore not uncommon for one machining concept to include hundreds of pieces of detailed information or machining steps or more. This includes numerous variant-specific machining solutions for every component. "Our goal is to offer a complete solution for 80 percent of the different variants of a component - all documented down to the finest detail, partly standardised and accessible to our specialists at all times."
(Continued on next page)