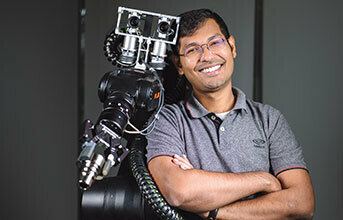
What are the new digital (automation and robotic) technology solutions you offer to your clientele?
Currently, CynLr is actively engaged in reference design collaborations with prominent manufacturing industries and giants within the automotive and machine tool industries. Together, we are focused on solving the hardest automation problem that demands very high dynamism and adaptability - part-mating and assembly. With our proprietary vision and grasp technology, our objective is to empower robots to be as dynamic and versatile as humans, when it comes to performing tasks involving object manipulation.
We firmly believe that achieving this goal will act as a catalyst for disrupting the manufacturing, and warehousing industries. By replacing the complex variety of machinery for every task to a uniform "standardised" visual robot across all tasks in a line, we aim to simplify the manufacturing infrastructure. This concept is known as ‘Universal Factories'. The factories of the future will be characterised by their adaptability, streamlined operations, and cost-effectiveness. We envision that our visual object technology will bring about transformative changes in the functioning of universal factories while revolutionising traditional processes and enhancing overall efficiency and productivity of the businesses.
Do you think manufacturers are still hesitant in integrating new age technologies to their facilities?
Surprisingly manufacturers are investing heavily on automation and more importantly on advanced manufacturing motivated by onshoring. The perspective on manufacturing changed after Covid, especially. When supply chains were disrupted, people realised that manufacturing is the ultimate backbone of any economy and building capacity is extremely important. Recognising this potential, conglomerates worldwide have already embraced new-age technologies and embarked on the path of smart manufacturing - integrating automation, robotics, artificial intelligence (AI), and the Internet of Things (IoT). However, in India, a significant number of manufacturers still face challenges in incorporating automation into their business models and struggle to transition into the new industrial revolution driven by automation.
We think that it is the perception problem that keeps manufacturers from automating their operations. Robots are universally considered to be a tool to cut/reduce costs. Instead, it should be viewed as tools for value creation. It's perceived otherwise because value is associated with the produce and the scale of produce, while manufacturing is seen as the cost for the produce. That's because the whole manufacturing infrastructure is often and always rigidly built to produce a specific product. Instead, if the factory could produce even a new design of product out of the same machinery, the capital expense on the machinery would suddenly be treated as investment, instead of cost and manufacturing will become the centre of value creation.
Our customer base mostly includes specific sectors in manufacturing such as automotive, electronics, white goods, aerospace, jewellery, some use cases of e-commerce warehousing and logistics. Customers who are looking to automate previously non-automatable tasks can do so using CynLr's visual intelligence. Our platform enables simplified deployment with no need for hardware customisations from task to task or object to object. CynLr's robots can be deployed 70 per cent faster with 30 per cent lower costs. The biggest benefit is that they are adaptable and not tied to a specific product.
How do you ensure compatibility with different manufacturing processes or software platforms?
Our groundbreaking visual object intelligence platform empowers industrial robotic arms to see, comprehend, and manipulate objects in random and unstructured environments, offering a comprehensive solution for automation and object handling.
So, our product is highly dynamic and adaptive. It obsoletes the need for customised solutions. Customers don't have to deal with learning 30+ technologies, designing complex custom design engineering and a long strenuous cycle of research and validation for even simple tasks. We ensure this by using cutting-edge techniques such as Auto-Focus Liquid Lens Optics, Optical Convergence, Temporal Imaging, Hierarchical Depth Mapping, and Force-Correlated Visual Mapping in our hardware and algorithms. These AI and Machine Learning algorithms enable robotic arms to perceive and generate rich visual representations, allowing them to manipulate and handle objects based in any environment.
Kindly provide an estimated return on investment (ROI) that clients can expect from your products and services.
There are well established benchmarks to determine the cost of automation, especially when they are seen as the direct cost replacement for labour wages. But that's hardly ever the reason for industries to automate. The cost of non-synchronous production that leads to unpredictable output, demanding heavier stocking, complex inspection process and the cost of recall in the automotive industry are the major drivers of automation.