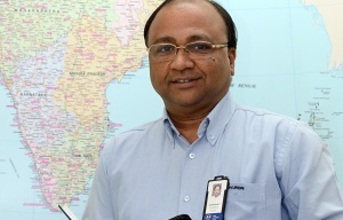
Focus on quality
At Maruti, Sarangarajan brought in the concept of quality consciousness and helped in improving quality levels and bringing in the best practices to the shop floor of the ancillaries. In the next decade with that company, he successfully implemented the concept of quality assurance of products and processes at Maruti and their vast network of 400 plus vendors.
Leveraging on this huge experience, Sarangarajan has introduced a number of systems working in close co-ordination to ensure that HMI gets flawless quality. "At Hyundai, we have invested heavily in technology to ensure that nothing is left to chance or luck. Nothing is kept open to interpretation. For example, we have inter-linked torque systems which ensure the needed torque is applied on the critical assembly of parts. If the torque is not achieved, the conveyor line will stop and everyone in the plant, including our MD will be alerted!"
Similarly, the plant has automated inspection system where the engine is inspected for some 60 critical parts and assemblies and if even one is missing, the engine will not move to next station. "On the supply side, we choose vendors with technological excellence and who have proven capability in supplying top of the line products. This is especially pertinent since 85 percent of our components are supplier dependent. Once the products enter our system, we have 500 checkpoints manned by experienced and highly qualified professionals, who serve as our quality gatekeepers. These stringent measures help us maintain our quality," Sarangarajan explains.
Cost reduction
With increasingly intense competition, there is a lot of pressure on OEMs to keep their prices competitive. This involves reducing costs at the shopfloor level to start with. How is Sarangarajan doing it at HMI?
"We have been able to achieve cost competitiveness by keeping a strict control over our internal costs of production, controlling cost of utilities and through a high degree of indigenisation. We have a system called the ACT 302*, where every member on the shopfloor is encouraged to think of ideas to save costs. Last year, we carried out more than 4,000 projects on the shopfloor itself which resulted in the savings of about Rs400 million! On the utility side too, we have a target of reducing the cost per car by 3-4 percent annually, year on year. Our suppliers also work on similar lines and hence collectively we have been able to achieve a tight control on costs." (*ACT 302 is aimed at improving productivity by 30 percent in two years and hence the number).