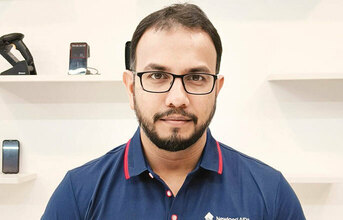
Lean manufacturing could be defined as a key methodology that focuses on minimising waste within the manufacturing system while simultaneously maximising productivity. Thus, it addresses one of the worst things that could happen to any company: ‘Wastage'.
Unfortunately, waste is a common occurrence when we talk about the manufacturing industry, whether it is an inefficient workforce, inaccurate production lines, or unutilised material due to poor inventory management. Lean manufacturing plays a significant role in combating this burgeoning issue. While it primarily focuses on minimising waste, it also aids in boosting customer value and, along the way, helps with process improvement using various lean principles and techniques.
The concept of lean manufacturing was coined by Ohno Taiichi, a Japanese industrial engineer and businessman, also known as the father of the Toyota Production System (TPS).
Lean manufacturing has also proven positive in bolstering the sustainability and operational economic performance of manufacturing industries by eliminating non-value-added operations.
5 key principles of Lean Manufacturing
The success of optimised lean manufacturing revolves around these five principles. These include:
Value: While value is created by the producer, it is defined by the customer. Thus, it is necessary for companies to understand the value that a customer places on their products and services, which, in turn, can help them determine how much money the customer is willing to pay.
Value stream: Analysing and mapping the flow of information or resources is required to produce a specific product or service with the intent of identifying waste and methods of improvement, as value stream mapping encompasses the product's entire lifecycle, from raw materials through disposal.
Flow: To eliminate major functional bottlenecks and find routes to improve lead time, devising the flow plan is instrumental.
Pull: Lean manufacturing works effectively in a pull system. Hence, it is pivotal to identify new work that has good demand. Push systems also come in handy in manufacturing resource planning (MRP), for which the inventory needs to be determined in advance.
Perfection: The perfection in lean manufacturing lies in perpetually targeting the root cause of quality issues and curtailing the waste across the value stream until perfection is attained.
What is AIDC Technology?
Working on the same objective as lean manufacturing, i.e., maximising productivity and efficiency while reducing waste and shrinkage, Automatic Identification and Data Capture (AIDC) technology facilitates the automated collection of data to further enhance real-time accuracy and bolster traceability. The key AIDC identity markers are barcodes, QR codes, RFIDs, biometrics, optical magnetic strips (OCR), etc., which allow businesses to make better-informed decisions.
The significance and benefits of AIDC Technology in Lean Manufacturing
The global AIDC industry has already reached a market size of 49.8 billion dollars in 2022 and is forecast to reach 106 billion dollars by 2028 at a staggering growth of 12.6 per cent (CAGR), as per a study by IMARC, thanks to the adoption of rapid digitalisation and the incorporation of innovative automation.
Some key benefits are as follows:
1. Enhanced process efficiency
2. Real-time data capture
3. Improved inventory management
4. Improving accuracy and cutting down the degree of error
More importantly, AIDC identity markers like barcodes, QR codes, and RFID further play a significant role in capturing quick, real-time identification and resolution of quality issues and eventually aiding in better workforce productivity. For instance, factory workers equipped with mobile devices or wearable technology can access information about the production process, track the status of orders, and make informed decisions on the shop floor, thus fostering a culture of continuous improvement and empowerment.
AIDC technology works as a game changer with respect to traceability, which is a crucial part of the manufacturing process, while also ensuring it is aligned with industry standards and regulation compliance.
AIDC technology further integrated with lean manufacturing also helps in combating the biggest challenge of companies, which is cost cutting, as there is an immense saving from reduced labour, improved inventory management, and fewer errors, which eventually impact the bottom line.
When we talk about the marriage of lean manufacturing and AIDC, just-in-time, or JIIT, manufacturing is pivotal, which is a marquee production model where items are created to meet demand, not created in surplus or in advance of need. The key aim is also to increase efficiency, reduce costs, and eventually speed up product delivery.
The future of integrated AIDC led by Lean Manufacturing
In today's fast-paced and interconnected world, efficient workforce management has emerged as a decisive factor for businesses aiming to achieve unprecedented success. The era of digital transformation has not only disrupted traditional manufacturing practices but also presented a remarkable opportunity for companies to thrive in an increasingly competitive landscape. In the recent past, it has been established that AIDC technology is indispensable in the world of lean manufacturing. Their ability to streamline inventory management, enhance process efficiency, reduce errors, empower the workforce, ensure compliance, and provide valuable data for continuous improvement makes them a key component of lean manufacturing strategies.
The amalgamation of lean manufacturing coupled with AIDC technology will further aid in optimising operations, and with the adoption and leverage of modern technologies and automation, businesses in India will only grow and be poised to achieve better efficiency and competitiveness in the global markets.