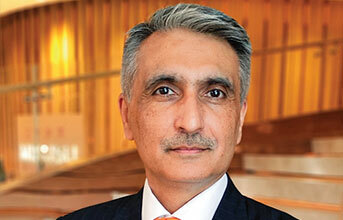
Sumit Kumar, Chief Business Officer, TeamLease Degree Apprenticeship
With the recent elections securing a win for Government 3.0 under the leadership of Prime Minister Modi, India's strategic drive to position itself as the world's manufacturing epicentre is expected to gain ground. India is emerging as a formidable contender for the China+1 strategy, capitalising on a unique convergence of factors. But India is still grappling with critical policy gaps in its industrial strategy, compounded by a looming skill deficit. According to World Bank data, less than three per cent of global manufacturing currently occurs in the world's most populous country, a stark comparison to China's commanding 24 per cent share.
In alignment with its ambitious vision, the Indian government aims to augment the nation's share of global manufacturing to five per cent by 2030, with a loftier goal of 10 per cent by 2047. This aspiration underscores India's desire to solidify its status as an indispensable player in the global economic landscape. India's ascension as the world's fastest-growing major economy, buoyed by a burgeoning tech sector, is undeniable. However, juxtaposed with this economic dynamism is a traditional economy struggling to generate sufficient employment opportunities. The confluence of these dynamics presents both promise and peril, encapsulating the essence of the three Ds: de-risking, diversifying, and decoupling. In the wake of a reordering geopolitical situation with far-reaching ramifications on the geo-economic landscape, the imperative for derisking, diversifying, and decoupling has assumed paramount importance. Today, pursuing a China+1 strategy reflects a broader global sentiment favouring a strategic pivot away from over-reliance on a single country and supplier. However, strong policies and a skilled workforce are needed to further this momentum.
Skill deficit: A hurdle on India's path to manufacturing process
With the government's relentless pursuit to establish India as the hub for Electronics System Design and Manufacturing (ESDM) under the Make in India campaign, several initiatives have been set in motion. The National Policy on Electronics (NPE) 2019 serves as the guiding framework, complemented by strategic incentives such as the Production Linked Incentive Scheme (PLI), the Scheme for Promotion of Manufacturing of Electronic Components and Semiconductors (SPECS), and the modified Electronics Manufacturing Clusters Scheme (EMC 2.0), alongside the PLI for IT Hardware. These initiatives aim not only to bolster the industry's competitiveness but also to catalyse its growth trajectory.
While the electronics manufacturing sector currently employs around 3.5 million professionals, its expansion promises to generate 3.3 million more employment opportunities in the next three years. However, it concurrently grapples with the persistent challenge of a skill deficit, highlighting the critical and ongoing need for concerted efforts in building and enhancing a skilled workforce. The success of India's foray into electronics manufacturing hinges on infrastructural and policy support, along with the availability of a proficient workforce capable of driving innovation, efficiency, and competitiveness. Therefore, addressing the skill deficit is essential to fully capitalise on the sector's growth potential and ensure its long-term sustainability.
In addition to bridging the skill gap, India's ambition requires a focus on upgrading technology and ensuring product quality. Learning from China's strategy of leveraging partnerships for technology advancement is crucial. This emphasis on technology must go together with stringent quality control to avoid incidents involving substandard products that have previously tarnished the "Made in India" brand. The confluence of advanced technology, skilled professionals, and uncompromised quality will be critical determinants in realising India's manufacturing potential and ensuring sustainable economic growth.
Bridging the skills gap
The development of skills is crucial for minimising risks, expanding diversity, and reducing dependencies in the electronics industry. India's goal of becoming a global electronics manufacturing hub depends on its ability to address skill shortages and enhance technological capabilities. The recent approval of $15 billion in investments for three semiconductor plants underscores the success of government schemes. The Production Linked Incentive (PLI) scheme, in particular, offers a $1.7 billion incentive package for companies establishing semiconductor manufacturing facilities in India, significantly boosting the industry's capacity and potential for job creation. The government's support is instrumental in creating a conducive environment for the industry's expansion and in addressing the talent gap.
According to our internal projections, the semiconductor industry may face a shortage of 250,000 to 300,000 professionals by 2027. In addition, there are expected to be 600,000-700,000 openings in EMS roles, 50,000-60,000 in the wearable technology sector, and a demand for 400,000-500,000 professionals in circularity and e-waste management roles across R&D, design, manufacturing, and advanced packaging. It is crucial to address this gap, as relying solely on technological advancements or infrastructure improvements will not be enough. The success of India's electronics manufacturing capabilities depends on the convergence of technology, skilled professionals, and quality. Therefore, strategic planning and collaborative efforts are essential to ridge the skill deficit and ensure sustained growth and competitiveness in the electronics manufacturing sector, especially considering the need for de-risking, diversifying, and decoupling in this context.
The Electronics Sector Skill Council (ESSC) has been actively offering over 35 apprenticeship courses under the NAPS scheme to address skill shortages at various levels of entry-level work. The number of apprenticeships in the electronics industry has surged from 7,517 in 2019-20 to 91,948 in 2023- 24, marking a remarkable 12.2-fold increase. This surge in apprenticeship participation highlights the potential of such programs to contribute to the industry's growth and support the three Ds. By derisking through a diversified skill base, India can reduce its dependency on a single skill set or workforce segment, thus enhancing its resilience against global market fluctuations.
Degree Apprenticeships and Work Integrated Learning programs can further accelerate the learning curve and bridge the skill gap while providing onthe-job training. The manufacturing sector has also experienced a remarkable 6x growth in the demand for apprentices. Data from the National Apprenticeship Promotion Scheme (NAPS) portal illustrates a consistent upward trajectory in apprenticeship enrollments across various sectors, reaching 900,000 in the last year alone and approximately 2.826 million over the past six years. This surge underscores a growing interest among both employers and individuals in leveraging practical training opportunities to bridge the gap between education and industry needs.
The success stories from India's PLI scheme include Taiwan's Foxconn, the world's largest contract electronics manufacturer, investing significantly in expanding electronics manufacturing within India, aiming to create 100,000 jobs with a $1 billion investment. Moreover, Apple's iPhone production in India is expected to increase to 1 in 4 by 2025. Furthermore, Tata Group is partnering with Taiwanese universities to train Indian labour in electronics. These strategic partnerships emphasise the importance of decoupling from overreliance on any single source of technology or labour and instead building a robust, self-sufficient ecosystem.
While India has significant potential to increase its share of the global electronics market, there is still a long way to go. Realising India's potential as a manufacturing powerhouse requires a multifaceted approach, including robust policy frameworks, infrastructure development, and, most importantly, skill enhancement initiatives. Only through sustained investment in skilling and upskilling endeavours can help India secure its position as a formidable player on the world stage.