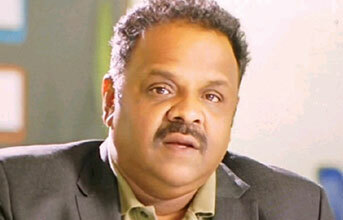
Automated Guided Vehicles (AGVs), such as guiding carts, tow tractors, robotic forklifts, and unit load carriers, enable warehouses to enhance efficiency. However, ensuring safe collaboration between autonomous vehicles and human workers is imperative as facilities integrate AGVs. Core safety measures for all AGVs involve emergency stop responsiveness, anti-collision sensors, speed control, and exhaustive testing. The safety features are also warranted by safety certifications. However, the robust functionality of these measures varies among different types of AGVs. Broadly, there are three important considerations for safety features, namely the integration of vision perception cameras, integration feed from surveillance cameras, and emergency braking.
We will first consider various certifications required, evaluate the important integrations, and then discuss individual AGV specifics.
IMPORTANT CERTIFICATIONS
Automated guided vehicles (AGVs) and their components require various safety certifications. For AGVs, key standards are ANSI/ITSDF B56.5-2019 (US) and EN ISO 3691-4:2023 (EU). Lidar sensors must comply with standards like IEC 60825-1 and certifications from ASPRS. Batteries need certifications to UL 3100 to ensure protection from electric shock and fire. Motors fall under overall AGV standards, with safety systems communicating speed/stop commands. Specific required certifications vary by region and application. It is important to consult with a professional to ensure these compliances are met.
INTEGRATION OF VISION PERCEPTION CAMERAS
Vision perception cameras are critical for enhancing the safety of Automated Guided Vehicles (AGVs). They identify potential threats by continuously monitoring static and moving objects. By expanding perception range and reducing blind spots, they decrease accidents caused by insufficient perception. Perception systems greatly increase vehicle safety and climate resilience. Dash cameras analyse and map scenes to provide specific road safety warnings. Engineers aim to develop sensors and AI that outperform human senses fine-tuned by evolution. Running perception algorithms through labeled training data enables safe detection and reaction to diverse road conditions and objects.
INTEGRATING LIVE DATA FROM SURVEILLANCE CAMERA FEEDS
Surveillance camera feeds are vital for enhancing Automated Guided Vehicle (AGV) safety. Ceiling mounted cameras provide comprehensive environmental views to determine safe motion and avoid collisions. Cameras can swiftly detect and extinguish fires in industrial settings. Safety sensors prevent AGVs from hitting objects; camera feeds bolster this by enabling proactive risk avoidance. Surveillance helps governments uphold order, recognise dangers, and investigate crimes. So, for AGVs, surveillance bolsters operational safety and security. Overall, surveillance camera feeds are crucial for preventing accidents through extensive situation awareness, rapid-fire response, augmenting onboard safety systems, and strengthening industrial oversight. Their comprehensive real-time insights make AGVs safer.
AUTOMATIC EMERGENCY BRAKING
Automatic Emergency Braking (AEB) is a vital safety feature in Automated Guided Vehicles (AGVs). By automatically initiating braking, AEB can prevent collisions or reduce impact severity. With a quicker reaction time than humans, AEB saves lives through rapid response. As an advanced safety technology, AEB represents a huge leap in protecting against rear end collisions. AEB typically activates after a forward collision warning alerts the driver of an imminent crash. Reverse AEB reduces low-speed parking damage. Avoiding over 85 per cent of rear-end crashes, AEB is highly effective at decreasing collision likelihood and speed when crashes remain unavoidable. Overall, AEB dramatically enhances vehicle safety.
Evaluating each safeguarding dimension proves critical to understanding capabilities and limitations when operating alongside humans. By deliberately investigating safety measures in pace with rapid AGV adoption, warehouses can securely benefit from vehicle autonomy while protecting on-floor staff. We will now discuss the four most common types of AGVs:
AUTOMATED GUIDED CARTS (AGCs)
Automated Guided Carts (AGCs) are carts that autonomously transport materials by following predefined paths, using guidance systems like magnets or lasers. Key safety features include collision avoidance sensors to detect obstacles and emergency stop buttons to halt operation, if triggered. Assessments evaluate if proximity sensors maintain safe human-AGV distances and if alarms properly warn people. Navigation systems are tested for accuracy, while speed and trajectory adjustments are analysed. Emergency stops strategically halt and brake motors rapidly. Redundant sensors, often multiple laser/optical systems, ensure reliable navigation and system failover. Assessing if warning indicators, navigational stability, emergency responsiveness, and redundancy measures collectively enable safe autonomous transport alongside people is critical.
AUTOMATED GUIDED TRACTORS
Tow tractors haul multiple carts, requiring considerations around towing dynamics, intersection movements, and collision avoidance. Redundant sensors, including backup detection and navigation systems, enhance reliability. Examinations evaluate sensor coordination competencies to maintain safe operations during emergencies or malfunctions. Emergency stop buttons trigger braking to halt tractors and loads. Assessments analyse dynamic path planning abilities, verifying real-time route optimisations and obstacle circumventions. Tests check alarm light placements and signal clarity. Advanced technologies like laser scanners facilitate navigation, while load monitoring prevents overloading. Further criteria involve fusion and communication across sensors to enable coordinated load manoeuvres. By investigating emergency responsiveness, alarm efficacy, navigational stability, obstacle avoidance, and load balancing, facilities can validate tow tractors offer innovations to safely operate alongside personnel.
AUTOMATED GUIDED FORKLIFTS
Robotic forklifts autonomously lift and organise pallets using arms and sensors. Key safety factors involve maintaining stability when stacking variable loads at height while detecting layout changes and obstacles in warehouses. Redundant cameras, lasers, and proximity sensors enhance spatial awareness and precise manoeuvring. Assessments analyse obstacle detection and avoidance abilities, verifying if forklifts can navigate around impediments. Examinations evaluate abilities to sense load sizes for tailored movements and detect human presence to trigger safety protocols preventing accidents. Alarm lights convey real-time status during loading, transitions, and duress. Emergency stops prominently halt all systems to freeze position. Further criteria investigate dynamic route optimisations based on environmental fluctuations and sudden obstacles. By scrutinising sensing capabilities, alarm integrations, emergency responsiveness, and redundant vision modalities, facilities can determine if forklifts safely collaborate with staff.
AUTOMATED GUIDED UNITS
Unit Load AGVs safely transfer defined load types like pallets using redundant vision systems and sensors to heighten load detection and navigation accuracy. Examinations verify adaptation competencies across varying conditions. Emergency stops rapidly halt motors to safely brake cargo. Assessments evaluate load-specific sensors to handle freight and collision prediction algorithms that model trajectories. Safety zones triggering deceleration are analysed. Alarm lights indicate status changes during transitions, loading/ unloading, or obstacles. Additional evaluations examine load monitoring sensors maintaining cargo stability, environmental sensors enabling navigation adaptations, and communication systems for coordinated inter AGV movements. Safety scanners detect obstacles and humans, slowing or stopping AGVs accordingly, enabling human-robot collaboration. By investigating emergency responsiveness, alarm integrations, redundant sensing, and load/environment monitoring, facilities can determine if AGVs provide layered innovations to operate safely around personnel.