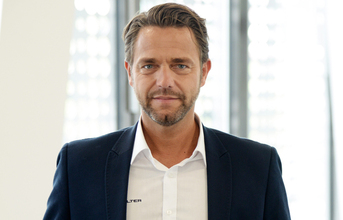
Further development of the tooling systems
The challenge: Titanium is more difficult to machine than aluminium, which has largely been used until now. Its high chemical reactivity leads to chips becoming fused at the cutting edge during machining. The poor thermal conductivity of the material allows temperatures at the cutting edge to rise significantly. The resulting chips are often extremely tough and abrasive. The minimal modulus of elasticity leads easily to the workpiece bending. Together with material solidification in the edge zone, this reduces the tool edge life even at low cutting speeds.
The tool costs also significantly depend on the demands placed on the component and the material, as well as on the process. Decreasing the wall thickness can cause the parts to become extremely unstable, thus an important focus is the stability of the machine and the clamping. Using the right coolant strategy also has a significant influence on tool life. Walter is continually developing its tooling systems with the aim of reducing machining times. Carbide substrates, new coating technologies and macro- and micro-geometries of the cutting tools play an important role here. The machining strategy can, however, also be further optimised in collaboration with CAD/CAM specialists.
This all makes high-performance cutting (HPC) and high-dynamic cutting (HDC) for finishing and roughing titanium possible today. Dynamic milling with the Walter Prototyp Ti38 Z6-10 and innovative new coating enables cutting speeds of up to 140 m/min to be achieved. Multi-tooth solutions with up to ten teeth allow the feed to be increased by up to 50 percent at low contact widths. These solid carbide tool solutions can ultimately achieve an increase in metal removal rate of up to 50 percent in comparison with conventional solutions.
(Continued on the next page)