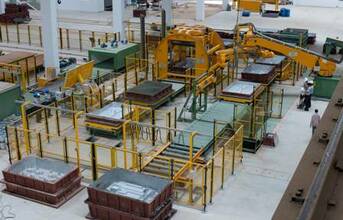
The moulding area is equipped with a continuous sand mixer of 60 MT capacity, compaction table, fast loop, rollover machine, infrared oven, painting station, gas drying oven, closing station, pouring and cooling line, mould pusher and shake-out. One of the specialties of this foundry can be observed in the moulding area - it uses cake moulding so that the need for moulding boxes is eliminated. This creates a direct positive impact on cost, time and space.
From the moulding area, the sand is sent back for reclamation. This process will be carried out with the help of pneumatic transport - ensuring the atmosphere within the foundry stays sand-free. The core shop, melting and fettling areas and last but not the least, the laboratory, comprise the rest of the foundry. The core shop comes with a continuous sand mixer of 10 MT capacity, carousel, core handlers, painting station, drying ovens and storage area. A dual track induction furnace with 4 MT capacity along with a melt manager will comprise the melting area. A hybrid shot blasting machine will be used for fettling. Reducing stress on castings is a major objective - and to achieve this gas fired furnace equipped with computer control will be used. Primering of castings will be done within a painting booth so that safety concerns are taken care of.
Quality issues are a reality and so are rejections. Keeping these aspects in mind, Ace Designers has set up a state-of-the-art laboratory to accompany the foundry. The lab is equipped with a spectrometer, carbon silicon apparatus, universal testing machine, microscope, impact tester, hardness tester and a variety of sand testing equipment.