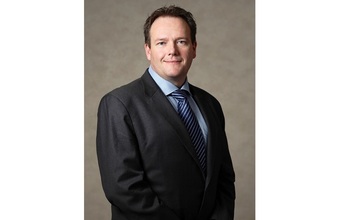
Manufacturing companies today face the Herculean task of protecting the lives of their employees while also safeguarding business. This is possible only if they can restart the operations in the right way. What role do you see advanced technologies playing in enabling manufacturing industry to get back on track in New Normal?
You can look at this from a number of angles - the supply chain angle, the facilities management angle, and lastly the workforce management angle. By what we have witnessed, it was the supply chain industry which has observed immediate changes during these times and we have a few solutions that provide quality insights on what's happening in the global supply chains.
The factories in China were shut longer than usual post Chinese New Year and the supply chains were disrupted but it proceeded back to normal quickly and then the world shut down. The malls, shops, companies, retails stores and brands stopped ordering and became stagnant, giving rise to cash problem in the supplies and liquidity crunch. With a substantial amount of global trade being managed through the Infor Nexus supply chain platform and to deal with this scenario, Infor introduced two programmes- first is a visibility programme to provide real time visibilities & insights on tracking shipments and second is a supply chain financing scheme to provide buyers and suppliers with easier access to capital from lenders. The cash however was quite substantial, and the traditional bank was not sufficient to provide a trade finance so we had to bring in more trade finance companies to our supply chain.
Talking about facility management and getting the factories and offices back to work, the government has introduced mandatory policies and guidelines to follow like: safe distancing, new cleaning procedures and processes and instructions on how to deal with personal protective equipment. Infor offers Facilities Management Capabilities that provide transparent operations, regulatory and SLA compliance with correct regulatory labelling, effective cost management and long-term asset value to customers. Infor also provides procedures on maintenance and cleaning processes, which is normally done once a week and during the pandemic has changed to almost five times a day. We also provide case management in case a customer has an infected situation, not all companies have the infrastructure or systems in place to manage case management situations.
Lastly, we offer Infor Workforce Management (WFM). We observed that people still had to go to office or to their factory but in different situations. Therefore, to keep businesses healthy and at the same time ensure employee's safety, we provide companies with a workforce management solution that has time, attendance and rostering capabilities and provides information about relevant features and functionality that can help organization respond to COVID-19 and evolve in the new normal. So these are the three areas in which we are helping companies deal with the new situation.
Cloud solutions have been around for a while now but things have changed drastically now. Do you see increased use of the same due to the pandemic?
The pandemic has definitely fast forwarded almost five years of the digitization across a lot of sectors and the move to ecommerce, economy and cloud has gotten accelerated too. Cloud as a system is a secure platform and with the rising ransomware attacks, it is best for organizations to move their applications and data to cloud. Another aspect is artificial intelligence, which is now becoming the new normal that only works on a cloud environment, where you have a dynamic elastic scalability situation. And the last aspect is the speed of innovation which is high and one cannot keep up with that anymore in one's own data centers and also does not have the technology to manage it. The speed of innovation, security and artificial intelligence are key drivers for cloud and have seen an upsurge during the pandemic. How we help our customers is by consulting and supporting them and taking over the management of our customer's business application environment.
What role do you see innovation playing the given scenario? How can Infor help the industry on this front?
In the manufacturing industry, consumers usually want something new or extremely personalized which lays a lot of pressure on the manufacturers, demanding them to be flexible and agile in the nature of their business. This is why we want to help our customers in having an environment that is agile, flexible, and very consumer focused. There are two categories of customers i.e. one with low volume, high complexity and other with high volume, low complexity. These are two extreme situations and requires order management processes, product lifestyle management, design, manufacturing and an integrated supply chain. And that is how we want to help our customers within those two extreme situations, industries and supply chains and be extremely capable of helping customers manage in those supply chains. In recent times, it has become dynamic as offshoring becomes reshoring, as the geopolitical landscape is impacting supply chains. So the whole digital disruption stays a very important aspect. That's where we want to help companies and kind of outpace that disruption and being the company that is disrupting instead of being disrupted by the competition. However, it requires some flexibility and agile environments along with a leading edge thinking and technology to make that happen.
The manufacturing industry is extremely asset-driven and with Covid-19 restrictions, maintenance has become all the more critical. How can Industry 4.0 solutions help manufacturers gain competitive advantage with predictive maintenance, remote monitoring and asset management issues?
Facility management for us is same as enterprise asset management, a solution that provides clean practices, preventive maintenance schedules, identifies the assets at risks, and helps to get ready for those changing expectations. The idea has always been to go from preventive to prescriptive, to maybe more autonomous. Managing assets has been a key aspect for us and that also has to be integrated when you cannot schedule a very important customer order, when you do a major overhaul of your production line. The order management process, selection planning process and the asset maintenance management process has to be in sync. Many companies are still in the reactive stage and there is a need to switch from reactive to preventive to prescriptive stage. With that, there is a need to monitor and measure consumption, duration, and wear and tear in real time. These are some of the key roles that asset management plays to help manufacturers. We also use that same tool to do the cleaning, scheduling and then labelling since labels are important to tell which area is at risk and the area that needs to be decontaminated. So, we provide all these work processes and procedures into a manufacturing environment.
But COVID-19 has completely revolutionised the whole world including the manufacturing industry. So, can we actually say that we are ready for Industry 5.0?
Not yet, I believe companies need to be extremely agile and ready for the change to welcome industry 5.0. For example, if retail and warehouses are down and the source is still operating, one can do direct to consumer shipments, so companies need to become agile to deal with that situation. Black swan events are completely disrupting what we are expecting, thus companies need to think completely different. However, companies are adjusting extremely fast and we see many of our customers moving into the direct to consumer trends. We see e-commerce adapting to this change, now even the local bakery not only needs to have a website, but also has to have an e-commerce platform from where customers can place an order. Every mom and pop store is almost needed to be online; companies are adopting new tools and techniques very quickly.
The automotive industry was already in some interesting movements, from battery electric vehicles - to autonomous vehicles. These are some key trends in automotive, so the automotive industry was already undergoing a big disruption and then you get such an event on top of it. How to deal with this change is very interesting and challenging for the executives in those companies.
Anything you would like to add?
I think as a company we offer very quick interesting programs across the globe as we also have very good visibility in Europe and Asia. We have got a lot of interest in those programs that we came up with because they are so essential in helping customers in dealing with some of the new challenges.
END