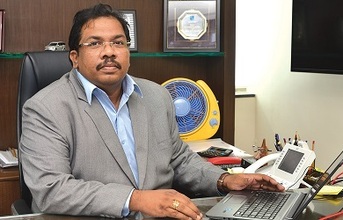
How do you benchmark yourself?
The Mahindra Automotive Division has seven major plants in India and one in Korea (SsangYong motors). We have a similar set up for tractors. In a way, we have more than enough plants internally to benchmark as every plant has one or two areas of excellence.
Benchmarking for us works in two ways, internal and external. When we say internal we mean within our plants we compare similar shops and processes with respect to various efficiency parameters and we do the same with our other plants in the group. Example, a vehicle rolling plant will have all its parameters compared and benchmarked with all our plants across the group in India and globally. This builds a healthy internal competition. We also have synergy groups consisting of members from all plants who continuously interact and visit to keep this process strong, leading to continuous improvements.
On the external front we benchmark other OEMs, many a times visit the "best practice "companies.
We also work and partner with suppliers on latest technologies and processes that can be implemented in the near future. We not only learn from auto industries but also learn a lot from other industries remotely connected to us. Our teams are on the move across the world attending different technology seminars /shows scouting for something new to make us more efficient and effective. We work with industry experts on specialized areas, also we interact with various institutes like IITs and other research institutes.
Skilled workforce is the challenge before the industry? What initiatives are undertaken for the skill building and craftsmanship, which is a requisite in present times unlike in the past when it was about basic manufacturing?
Hiring the right talent coupled with right training soon after on boarding is the key for skill development.
We have taken the "First time right" mantra to schools, we believe we must teach them the right skills from the very beginning to reduce the unlearning time. Therefore, we have partnered with couple of ITI's from our neighbourhood, we work with them proactively, help them on the right curriculum, the right equipment's so as to develop the right skills and talent even before they leave the school. This model has helped in addressing the needs of our Industry and is focused on making students work ready.
Once in the factory our focus shifts to training them for skill and finesse or craftsmanship, for which the employee undergoes an elaborate hands-on training program in our domain wise dexterity schools aptly called "GURUKUL" where expert trainers hone their skills before they are deployed to work in production. We are able to simulate the actual working condition in production in these Gurukuls.
Internally with an objective to further enhance the manufacturing skill standards at Mahindra to a Global level the program on Mahindra Skill Excellence was initiated. The program aids the skill building process, by exposing our workforce to the most stringent skills standards and subsequently equipping them with best-in-class training.
This initiative has brought lots of laurels in India and abroad. Results of these rigorous trainings and skill building programmes can be clearly seen from the fact that for last three consecutive competitions, our welder's have been selected at National Level and have represented India for the World Skill Competition at Germany, Brazil and the upcoming World Skill Competition at Abu Dhabi due in Oct 2017.
In addition, we also do many behavioural and motivational programs with our associates. Apart from this, we also work on capability development of our associates by conducting internal & external competitions. The idea is "Right skills need to be complimented with the Right will to deliver excellence".
(Continued on the next page)