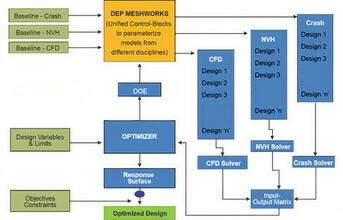
Increasing emphasis and high expectation on the fuel economy standards has pushed automotive OEMs globally to optimize their vehicle platforms. Fuel economy standards have to be achieved with holistically balancing safety, NVH and durability performance regulation and requirements. With competitive markets and compressed time to market needs, OEMs are looking for technologies that enable them to cut short their development time or make their current platforms more efficient. All this of course, has to be achieved with no degradation of performance. Another factor that is to be considered is that the above must be achieved with minimum packaging and tooling changes- if these can be kept constant while rolling out a new product line, it would be an excellent saving mechanism for any automotive manufacturer.
One place that can have a significant direct impact is to reduce weight from the BIW and chassis of a vehicle. Techniques like full vehicle parameterization and Multi- Disciplinary Optimization (MDO) can be utilized in shaving off the weight, keeping the other parameters constant.
MDO in Vehicle Development
Vehicle body structures and sub-systems need to be designed to withstand multi-disciplinary load cases such as crash (non-linear transient), NVH (frequency domain), stiffness (linear static), durability (linear static) and aerodynamics (CFD). The structural requirements to meet loads in one discipline are very often detrimental to requirements for loads in other disciplines. Unless loads from all disciplines are considered simultaneously during the optimization process, the resulting design will not be well balanced for structural performance. With the focus on vehicle fuel economy, carrying out optimization to reduce weight while meeting the performance targets for all the above varied load cases is of paramount importance. Multi-Disciplinary Optimization (MDO) is essential to achieve this objective.
Challenges in the Current MDO Process
The inability to adopt MDO as a step in the mainstream vehicle development process stems from the process limitations that have traditionally made the MDO process time intensive. Typical challenges encountered during full vehicle MDO exercises include:
Parameterization Time
The faster turnaround of an MDO project hinges on the ability to introduce different class of design variables in the full vehicle FE models with all their complexities. Usually these complexities of a full vehicle model counterweigh the faster execution of parametrization activity.
Multi-attribute Model Synching
Once the parameters are defined on any one FE model, for example the NVH FE model, there should not be any need to re-define them for other attribute FE models like safety FE models. Traditionally the need to recreate these parameters for other attribute models has created a bottle-neck in the MDO process timing. Parameters applied on one attribute model such as a crash model should be efficiently and automatically applied to other attribute models such as NVH and durability models. If attribute models are ‘synchronized' then this is achievable.
Design Generation Time
Job submission schemes may do a good job for one design at a time. However automated schemes are required to carry out the same analysis on multiple designs (for example the designs derived through a DOE). Using the parametrized CAE models, runnable analysis models for hundreds of designs need to be generated in an automated fashion.
Computation Time
One of the longest activities in the MDO process is the run-time taken by the solvers. Faster computing facilities with multiple CPUs and associated solver licenses are crucial for completing the analysis within the available time.
Automated Post-processing
There needs to be an automated process for extraction of results from different runs. Post-processing the results from hundreds of jobs without any scripts is a major hurdle in achieving a faster turnaround time for MDO.
Automated MDO
The automated MDO process consisted of a set of tools and processes that are used to facilitate faster project turnaround. The process starts with model synchronization- where full vehicle safety, trimmed body NVH and durability models are first unified and then synchronized. The models are then parameterized and one of the unified/synchronized FE models is selected and nominated as the ‘donor' model. A comprehensive set of shape, section, gage, welding parameters are created on this donor model. These parameters are automatically transposed on all the other attribute ‘driven' models. Design generation follows, where a Design of Experiments (DOE) matrix with the Optimal Latin Hypercube sampling technique is generated, discretizing the entire design space. Using software like DEP's Meshworks, crash, NVH and durability models are automatically generated for every design point of the DOE matrix. Optimization follows to find the best solution. The post-processed results are tabulated in the form of an input/output matrix where the input is the parameter values and the outputs are the responses. Using the input/output matrix, a Response Surface Model (RSM) is generated by fitting all the responses. Using the RSM, several optimization scenarios are carried out to pick a suite of optimal solutions. This entire process can be executed to complete the MDO in a few weeks.
Key benefits of the Automated MDO process
High degree of automation
As demonstrated by the above vehicle program application, this process is capable of generating and submitting several hundred designs, analyzing and postprocessing the results with a high degree of automation. This is a major enabler to execute the MDO in a short time as always desired to have an impact on the vehicle design.
Practical application to vehicle development
Earlier MDO processes that are not automated to this extent were typically executed only once during the life of a vehicle development phase due to the long execution time. Often Single Disciplinary Optimization (SDO) was carried out to identify the weight savings opportunities resulting in sub-optimal designs. In contrast, this process can be applied in a practical manner during every design cycle of the vehicle development.
Wide range of design parameters
The process outlined here allows for the selection of a wide range of parameters spanning various categories such as shape, section, gage, material, features, welding etc. thereby maximizing the design space exploration and hence the possibility of converging towards a true optimal solution. Further, this provides the opportunity to optimize the vehicle structure from the early stages of the vehicle development until the design is finalized for the verification prototype.
Automated synchronization across attribute models
Synchronization saves enormous time in not having to repeat the parametrization on each attribute model. It also minimizes errors during the parametrization step.
Rapid throughput
Generating and processing hundreds of design combinations within a very short time provides a wealth of data from which several useful design alternatives can be explored.
Weight saving while balancing performance
Since the process considers multiple load cases spanning multiple disciplines, a truly optimum solution with significant weight reduction can be achieved while simultaneously balancing performance for crash, NVH, stiffness and durability.