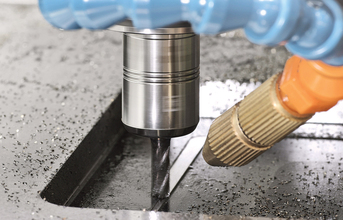
Straightaway to a perfect finish and perfect quality: What in the past would have been hardly conceivable in milling is now becoming a regular trend due to modern machine concepts and tools. The number of precision applications in which milling is no longer followed by grinding, polishing or eroding is growing continuously. In these applications the toolholding systems perform several tasks: they ensure exact run-out accuracy of the tools, compensate vibrations, and guarantee both high geometric precision and perfect surface quality.
Whether in the watch and clock industry, machine making or medical technology: in virtually all machining disciplines, companies are searching for efficient ways to streamline processes. Especially manufacturers who use ultra-precision machining processes, in which the engravers and finishers put the final touch on surfaces by hand, are pioneers in this respect. In view of machining times of up to 100 hours for a single workpiece, investments in innovative machine concepts, air bearing spindles, and modern tools pay off quickly - assuming the high precision of the machine is retained all the way to the cutting edge. The toolholding systems play a decisive role in this connection.
Mirror finishes with precise geometry: The levels of quality that can be achieved with precision machining nowadays fascinate even experienced users. Often the quality that can be achieved is equal to the results of eroding, grinding, polishing or laser-beam machining, yet much faster and therefore more economical. Test series with an aerostatically surface guided ultra-precision machining center at the ETH Zürich show that a consistent surface quality of Ra < 25 nm can be achieved with line-by-line milling, and Ra < 3 nm with surface milling. These levels of quality correspond to polished surfaces, and also exhibit high-precision geometry. While injection molds for high-gloss plastic parts in the past were first milled and then finished using an intricate polishing process, today it is possible to produce objects with extremely flat and smooth surfaces during the precision machining process. The effect is even more pronounced in the case of non-ferrous metals: through milling alone with diamond tools, it is possible to achieve geometrically precise mirror-finish surfaces that are suitable for use in laser optics, for example. The result is a combination of several effects: the time-consuming process of finishing is reduced significantly, while reducing the risk of convexities occurring or corners being rounded during grinding and polishing.
(Continued on next page)