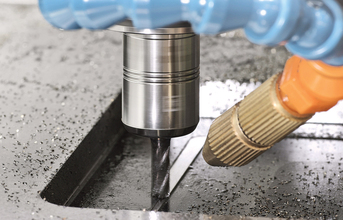
Wear-free clamping: Conventional toolholding systems, such as collet chucks or heat-shrink toolholders, generally are not capable of such demanding machining tasks. Users repeatedly complain of chatter marks, damaged tools, imprecisions
in the workpiece and concentricity errors, which are caused by minute contamination of the clamping faces. However, SCHUNK TRIBOS polygonal clamping technology features special properties: even the standard version of the patented technology from SCHUNK, the competence leader for clamping technology and gripping systems, achieves run-out and repeat accuracy of < 0.003 mm with an unclamped length of 2.5 x D, and a balancing grade of G 2.5 at 25,000 rpm. Since TRIBOS polygonal toolholders have no moving parts, they are not mechanically sensitive, and therefore ensure virtually maintenance-free and wear-free clamping. Even after several thousand clamping set-ups there is no material fatigue. In addition, they feature excellent vibration damping. With a hydraulic toolholder, tool change is achieved with minimal cleaning within a few seconds, to ensure a stable process. Depending on the type, the toolholders, which are suitable for all tool shanks in h6 quality, have been tested at speeds up to 205,000 rpm. Even tools with very small shank diameters starting at 1 mm can be clamped and changed while maintaining process stability.
(Continued on next page)