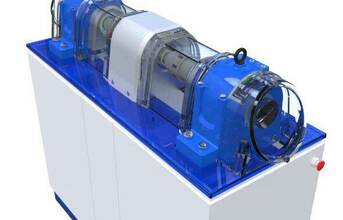
Our Insight technology programme is a new paradigm in condition monitoring focused on measuring parameters that detect damaging operating conditions rather than incipient failure. A key development enabling this approach is the use of a wireless sensor package, integrated into the bearing to record critical parameters that enable a customer to plan intervention to prevent rather than predict bearing failure.
This technology innovation is the culmination of more than 100 years of bearing applications and 30 years of experience in condition monitoring. We take a Life Cycle Management approach to our technology platforms and industry knowledge and combine them to work with customers, understanding their needs and demands.
It was out of this approach that we became interested in developing an integrated, self-powered sensor package that could communicate the operating environment to which a bearing is subjected. Following extensive R&D work, including miniaturisation, solving power generation challenges and developing unique packaging of sensors and electronics, the Insight programme made its official debut during Hannover Messe, Germany, in 2013. With this technology condition monitoring becomes autonomous: It powers itself, and it talks to the Internet. That enables it to be deployed in applications that were never before possible.
The project was born out of the fact that very few bearings fail in service as a result of normal operating conditions. Indeed, most in-service failures result from misuse, neglect, lubrication problems or operating conditions that were not foreseen when the machine was designed or the bearing specified.
Our engineers wondered what would be the outcome if a bearing could detect its operating environment - such as the actual loads it is being asked to carry, the quality of the lubrication, the temperature and so on - and make that information available through the Internet to the plant operator and/or the machine manufacturer. If operating conditions can be monitored, damaging operating conditions can be identified and corrected to make sure that expensive and disruptive failures are avoided, reducing the total cost of ownership and extending the life of the asset.