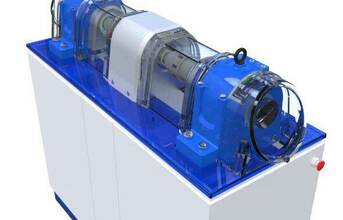
By combining integrated the Insight programme technologies with associated asset diagnostic and bearing health services, information relating to actual operating conditions is sent to cloud servers for remote diagnostics, enabling an understanding of the risk of future damage and failure.
Prior to our Insight programme, condition monitoring techniques could only monitor damage after it had occurred. Now, by sensing directly on the bearing, we can identify the risk of failure before the first microscopic damage has occurred, and with this information customers can take remedial action to avoid the cause of possible damage to the bearing - adding lubricant, mitigating transient overloads, etc. the Insight programme makes it possible to measure the loads the bearing actually experiences rather than what it was designed for. This valuable information can be routed back into the design phase to improve both the system and bearing design.
Improving accessibility
One of the purposes of the Insight technology is to make condition monitoring more widely applicable and accessible, particularly in applications where it has been considered impossible or impractical. This is one reason why the technology has been tested in challenging industries such as wind power, railways and steel manufacturing.
Wind farms can be remote and difficult to access. We are working with customers to integrate Our Insight programme technology and develop a smart bearing for wind turbine monitoring. This technology can wirelessly communicate dynamic bearing information to provide loads and lubrication operating conditions within its true operating environment. The cost of changing a wind turbine main bearing in an offshore application can be sufficient to undermine the business case for building the turbine in the first place. Therefore it makes business sense to record loads and lubrication conditions in service and take action to eliminate damaging conditions. It also may allow the turbine to be operated outside its design envelope when load and lubrication conditions are favourable. It is often the case that the most life-consuming operations will be conditions not included in the original design brief.
Within the railway industry we are integrating smart components and providing wheel end bearing monitoring solutions. Powered by the rotation of the bearing, these solutions can wirelessly communicate the bearing condition. In this application, the Insight programme provides a highly cost-effective means of collecting condition monitoring data, where the risk of failure for each bearing can be determined throughout its service life, allowing optimised maintenance planning and scheduling.
Similarly in the demanding and hostile environment found in the steel industry, we have developed a smart bearing solution that can monitor and communicate wirelessly the key parameters used to control and optimise the steel manufacturing process. It has successfully monitored the condition and operating environment of bearings in a continuous caster using embedded self-powered wireless sensors - an environment where cables and external sensors simply do not survive.
Conclusion
The focus of our technology development today is to reduce the environmental impact of an asset during its life cycle, both in its own and its customers' operations. The Insight technology will make condition monitoring more widely applicable, especially in applications where it was previously impossible or impractical. Maintenance can be scheduled before conventional condition monitoring picks up the early signs of a developing failure. Above all, by acting proactively to eliminate damaging conditions, failures can be eliminated rather than detected.
The author is Business Manager, SKF (UK) Ltd, Livingston, Scotland
END