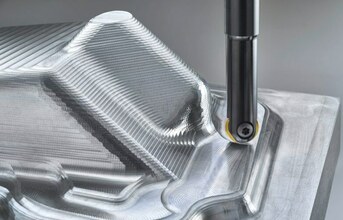
A combination of efficiency and precision
The engine experts at LMT Fette have created a comprehensive product portfolio for the various performance and quality requirements of gear cutting for vehicle transmissions through to drives in wind turbines. One hundred years of experience combined with the latest research and development results constantly generate innovative solutions to further reduce your costs per part.
This is how the new UNIFY indexable insert hob cutter came to be. It strengthens the area of application of the proven gear hob family CarbideLine-I (I= Indexable) in the module range from 6 -12 and is the preferred choice when high performance and high quality are a requirement for the machining of gears. The new design of the UNIFY has created a single-part, compact, very robust base plate which works with extreme precision due to the minimum number of interfaces. The compact design enables the use of indexable inserts for gear hobbing from a diameter of 150 mm which brings many benefits: It can be used on smaller machines, fewer limitations due to collisions and advantages with regards to processing time.
The new gear hob with indexable insert has already passed a crucial test in a practical application with flying colors. It was used for the machining of module 9 skew gears from 18 CrNiMo 7-6 material with 88 teeth and a gear width of 220 mm (figure 3).
The UNIFY which was designed especially for this application, used a protuberance plate with 4 cutting edges to achieve a gear quality of 9 with its first attempt. The smooth running and extremely even surface of the component as well as the short machining times impress the customer. The UNIFY combines precision and efficiency and has proven to be a new, strong partner for series production in the medium module range.
Modular tool life
Efficient internal thread production is the result of intensive tool research and repeatedly challenges the creativity of engineering experts anew. LMT Fette presented the first generation of HPF forming taps years ago and in the meantime has made a name for itself in the area of chipless internal thread production with its unique selling point of the modular design. HPF stands for High Performance Forming and combines the advantages of the wear resistance of a carbide thread head with the toughness of a steel shaft. This guarantees a new performance standard in terms of quality and cost-effectiveness.
Now, with the further developed HPF Max threadformer, an even higher performance dimension has been opened up (Fig. 4). In addition to the modular design, further significant design features are now making decisive contributions, especially the new micro-grain carbide, the new TiCN coating and the optimized former geometry.
The field of application of the HPF Max is in the serial production of the automotive industry and mechanical engineering.
END
For more information