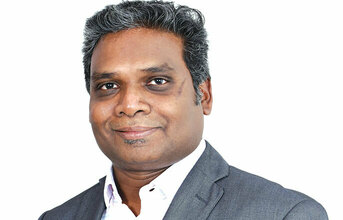
How is Duracarb India revolutionising the machine and tools industry with its one-of-its kind innovations and products?
Duracarb is a new IMC brand in India focusing on giving unmatched value for money to our manufacturing supply chain organisation. Manufacturing continues to grow in India, and with AatmaNirbhar Bharat, supply chain and SMEs, many new SME organisations are coming up and require solutions to increase productivity and reduce cost. Duracarb offers a complete range of precision metalworking tools and solutions covering Turning, Milling, Drilling, Parting, Grooving and Threading. With manufacturing facilities in Europe and Asia, marketing activities throughout the world, latest technology products and solutions from Duracarb help customers reduce their manufacturing costs and maintain consistent product quality.
Our advanced research & development initiative has also resulted in the quick introduction of new products and regular product upgrades. User feedback is incorporated in all stages of product manufacturing, to ensure precise and simple product selection without compromising performance, quality, and output needs.
Each Duracarb smart tool is crafted to the highest standards in state-of-the-art IMC facilities around the globe, including in Bengaluru, India. Our facilities comply with international standards, wherein our products and processes are certified for complete quality and environment management systems. Decades of knowledge acquired by IMC group on the formulation of basic carbides and coatings provide unmatched advantages for Duracarb R&D. Our carbide grades meet the exact demands of machining in shop floors of Automotive, General Engineering, Power, Aerospace, and many other industries. Our philosophy is to make the product easy to choose and easy to use, and at every stage. We ensure that the selection process is simple and user-friendly. We at Duracarb understand that the essence of a good tool supplier and customer partnership largely depends on timely availability of products. Our logistics system and distribution network fully support this need and ensures on time delivery. A well-trained network of application engineers and channel partners provide excellent after-sales service across the country all the time.
What sets your machining and tooling services apart from competitors in the industry?
Duracarb has a competitive edge over other players in the industry because of its adherence to the IMC standards in product design, which guarantee superior quality, performance, and reliability. With its dedicated customer support team that provides prompt and professional after-sales service across the country, Duracarb's products and solutions are designed to help customers reduce manufacturing cost and maintain consistent product quality. A strong research and development base enables Duracarb to introduce new products and upgrade existing ones regularly.
Tell us in detail about your R&D centre and how it helps with customisation of your products and services.
Duracarb India has a state-of-the-art research and development (R&D) centre in Bangalore, which is the hub of innovation and excellence for our company. The R&D centre is equipped with the latest technology and equipment to conduct cutting-edge research on various aspects of machining and tooling.
The R&D centre helps us with customisation of our products and services by:
• Developing new carbide grades and coatings that meet the exact demands of machining in shop floors of various industries. Our carbide grades are formulated with the knowledge and expertise of IMC group, which is a global leader in metal cutting solutions. Our coatings are designed to enhance the wear resistance, toughness, and performance of our tools.
• Designing new geometries and profiles for our tools and inserts that suit different applications and materials. Our geometries and profiles are based on user feedback and market trends, and they ensure precise and simple product selection, without compromising quality and output needs.
• Testing and validating our products and solutions in our own machining centre, where we simulate real-life machining conditions and measure various parameters such as tool wear, cutting forces, surface finish, dimensional accuracy, etc.
The R&D centre is also involved in several ongoing research and development projects aimed at improving the performance or introducing new features in our precision tools. This includes developing hybrid tools that can combine different machining processes in one tool. These hybrid tools can perform multiple operations such as face milling, shouldering, slotting among others with one tool. This enables us to reduce the number of tools required, save tool changing time, and increase productivity for the customer.
What are the new innovations you have introduced in your machine and tooling services and products?
Duracarb has developed new carbide grades and coatings that meet the exact demands of machining in shop floors of various industries. Duracarb's coatings are designed to enhance the wear resistance, toughness, and performance of its tools. Duracarb uses PVD and CVD coating methods according to material and component requirements.
Some of the coatings that Duracarb use includes:
TiN coating, which is a titanium nitride-based coating that provides excellent resistance to high temperatures, abrasion, and adhesion. TiN coating is suitable for machining steel, stainless steel, cast iron, and non-ferrous materials.
AlOX coating, which is an aluminium oxidebased coating that provides superior resistance to oxidation, diffusion, and thermal shock. This coating is suitable for machining high-temperature alloys, titanium alloys, and nickel-based alloys.
TiCN coating, which is a titanium carbonitride based coating that provides optimal resistance to wear, cratering, and plastic deformation. This coating is suitable for machining steel, stainless steel, cast iron, and hardened materials.
Duracarb has designed new geometries and profiles for its tools and inserts that suit different applications and materials. The geometries and profiles are based on user feedback and market trends, and they ensure precise and simple product selection, without compromising quality and output needs.
Some of the new geometries and profiles that Duracarb has introduced are:
Duracarb India works with a wide range of materials for machining projects, such as steel, stainless steel, cast iron, aluminium alloys, copper alloys, brass alloys, bronze alloys, titanium alloys, nickel-based alloys, high-temperature alloys, hardened materials, etc.