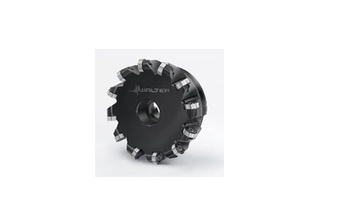
They also make the turbine housing the most expensive component in terms of machining. Buob explains further: "We anticipate different machining costs for each component, depending on the presence of an exhaust manifold." Above all else, a high chrome content reduces service life.
"There are applications where tools only last long enough for twenty to thirty components." For comparison: The materials used for diesel engine turbine housings extend the service life by up to five or ten times, while also being 50% faster to machine.
Walter machining experts have therefore developed a new milling cutter concept especially for roughing, semi-finishing and finishing turbocharger housings. It reduces the all-important cost per finished part, while also significantly improving surface quality.
Over the course of the development process, the cartridge system used for finishing, which had previously been the norm, was replaced with an intentionally simple tool design with a fixed insert seat. This "Plug and Play" solution eliminates the need to carry out presetting operations, which required accuracy to between 3 and 5 µm.
(Continued on the next page)