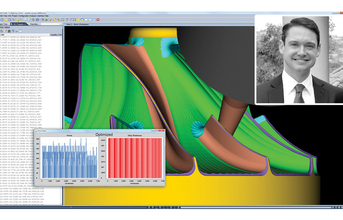
How does 3D machine simulation help shops engaged in aerospace manufacturing?
VERICUT software simulates CNC machining so that aerospace manufacturers can be more efficient, more competitive, and more profitable. A machine crash can be very expensive, potentially ruin the machine, and delay the entire manufacturing schedule. But with VERICUT, aerospace manufacturers can dramatically reduce the chance for error and avoid wasting valuable production time proving-out new programs on the machine.
CNC Machine Simulation detects collisions and near-misses between all machine tool components such as axis slides, heads, turrets, rotary tables, spindles, tool changers, fixtures, work pieces, cutting tools, and other user-defined objects. You can set up ‘near-miss zones' around the components to check for close calls, and even detect over-travel errors.
Today's NC machine tools process complex NC programs. VERICUT was designed by NC programmers and professionals in NC simulation and verification software, many of whom came from the aerospace industry. Because of this understanding and expertise, VERICUT is a powerful tool when using multi-axis machines, complex NC code, and/or advanced programming techniques.
VERICUT accurately emulates CNC control logic. Each control in the shop can be accurately simulated to account for different types of machines, programs, parts, and functions. VERICUT includes a library of flexible, easily modified controls from makers such as: Siemens, Heidenhain, Fanuc, and many others.
VERICUT features the most accurate collision checking available. Rather than just checking points along a path, VERICUT checks along the entire path of travel by sweeping through space. The user does not have to specify a "step size" tolerance that can slow the simulation if too small or miss the collision if too large.
Aerospace manufactures are currently under tremendous pressure to produce parts as quickly as possible. Late deliveries are unacceptable and many shops are already running at full capacity. With this in mind, there has been a lot of interest in CGTech's newest optimisation module: Force™.
(Continued on the next page)