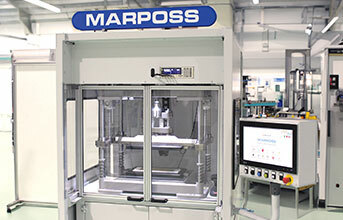
In the fuel cell and electrolyser industry landscape, precision and reliability play a fundamental role in ensuring optimal performance and efficiency of these systems.
Thanks to its constant innovation in the supply of advanced solutions for in-workshop control, Marposs allows manufacturers of these devices to achieve unprecedented levels of accuracy and quality in their production processes.
The company, founded in 1952, is a primary supplier to major automotive manufacturers that it is supporting in the transition to electric mobility, as well as to the aerospace, semiconductor, consumer electronics, refrigeration, and biomedical sectors. The group today has over 3,500 employees worldwide and is present with over 80 of its own offices in 34 different countries.
Marposs goal is to create quality control solutions for every stage of the production chain in both fuel cells and electrolysers, from the single component (flow plate, bipolar plate, catalyst, membrane, gas diffusion layer) to the balance of plant, the stack and then the complete fuel cell or electrolyser system.
Defects in any of the above products, both during production and assembly, can result in reduced reliability, efficiency, and performance of the fuel cell or electrolyser, as well as a hazards during their operation.
The analysis, identification and detection of these defects is addressed by the Marposs proposal, which is divided into solutions for gauging & inspection, leak, functional and electric tests.
Gauging & inspection applications are used to detect the geometric dimensions of individual components as well as to determine manufacturing defects due to pinholes, cracks, and assembly inconsistencies. The techniques are based on touch systems with probes and contactless systems that use optical technologies such as laser scanners, cameras, and confocal sensors.
Leak applications detect manufacturing and assembly defects of individual components as well as stacks and complete devices. They are based on the use of tracer gases such as He and forming gas (5 per cent H2 and 95 per cent N2) for vacuum chamber or sniffer tests using a mass spectrometer, or on the use of gases such as air or N2 for pressure drop and flow measurement tests.
A further alternative is the use of deionised water, especially in the field of electrolysers, to carry out tests under operating conditions and without leaving contaminating residues in the product.
Functional applications are at the margins of the production process and are preparatory for other types of tests. These include solutions for filling and emptying the stack with deionised water as well as solutions for determining the clogging of the bipolar plates (BPs) channels with air as the process fluid.
The range is completed by the electric solutions used to determine the characteristic curves and performance of the stack (mainly PEM or SOFC) or the fuel cell/ electrolyser system. In this area, we find applications for Interface Contact Resistance (ICR), Insulation Resistance (IR) and Dielectric Strength (DS) at high voltage, as well as applications for end-of-line (End of Line) controls such as open circuit voltage, control voltage pick-up, polarisation curve, Electrochemical Impedance Spectroscopy (EIS), performance, driving cycle and cyclic voltammetry tests.