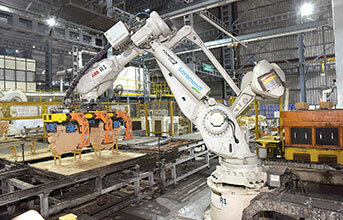
Swaraj Tractors, a prominent manufacturer of agricultural equipment in India, has recently taken a strategic measure to enhance its future readiness by upgrading its existing foundry unit to a state-of-the-art casting unit. As the Indian farm equipment sector is experiencing rapid growth, Swaraj Tractors is positioning itself to meet the growing demand for tractors ranging from 15 HP to 65 HP in India. The recently upgraded casting unit of Swaraj Tractors incorporates a range of cutting-edge practices that are firsts in the industry, including advanced automated systems, state-of-the-art technology, and lean manufacturing principles. This gives Swaraj Tractors a significant advantage over its competitors in the field of farm equipment manufacturing. The entire upgrade process took approximately two-to-two-and-a-half years to complete. After the upgrade, it took just two months to reach full capacity, thanks to the efforts of a dedicated workforce who were able to transition from an old manual system to a high-end automated one.
Advanced Automation and Lean Manufacturing Increase Efficiency
The Swaraj Foundry's state-of-the-art casting production unit is equipped with cutting-edge technology, including automated systems for mold, core making, and metal pouring practices. This reduces reliance on human skills and significantly increases the efficiency and accuracy of the production process. The incorporation of advanced equipment such as the latest induction furnaces, automatic pouring systems, and integrated quality control systems has also helped to optimise the process, increase productivity, and reduce costs.
The implementation of lean manufacturing methodologies has led to improved operational performance, shorter lead times, and increased efficiency, resulting in substantial cost savings for the manufacturers. It's worth noting that the Swaraj Division Foundry is the only captive foundry-of-itskind established by a tractor manufacturing company. The unit produces critical castings such as differential housing, gearbox housing, crankcases, and cylinder blocks.
Increased Capacity and Productivity
A world-class facility that has significantly increased Swaraj's casting delivery capacity from 120 metric tonnes a day to 200 metric tonnes a day, the Swaraj Division Foundry has set its sights on producing substantial quantity of tractors. The incorporation of advanced equipment, automated systems, and lean manufacturing methodologies, coupled with an integrated quality control system, has significantly increased productivity and efficiency, making Swaraj Tractors a leader in the farm equipment sector, both in India and beyond.
That said, the state-of-the-art foundry sets a benchmark for best-in-class foundries in India and abroad. The technical evaluation of these facilities has enabled the Swaraj Division Foundry to improvise and innovate to the extent that it has established new yardsticks and unmatched manufacturing standards in the industry.
Ultramodern Equipment Improves Working Conditions for Employees
The foundry has made significant improvements to its working conditions by replacing the traditional manual liquid metal pouring process with a state-of-the-art Automatic Metal Dispensing Press Pour Unit. This modern technology is coupled with VISIPOUR, an advanced predictive system that enhances the performance of the pouring process. The implementation of automation has significantly reduced dependence on manual operations, further improving working conditions and reducing fatigue for employees.
Improved Working Environment and Safety Standards
The foundry has successfully tackled the challenges of traditional manufacturing setups by implementing a new, streamlined process that minimises manual intervention at all stages of the casting manufacturing process. The result is a more efficient and streamlined working environment that reduces the physical strain of manual labour for our employees. The enclosed shakeouts, along with dust and smoke extraction systems, will significantly enhance the working environment in the plant by providing clean air and a safer workplace.
The new shop is fully compliant with European safety standards and features multiple interlocks that ensure a completely safe working environment. Additionally, safety fences that are interlocked with machines provide added protection for employees.