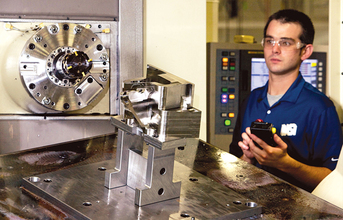
A seven inch long, one-inch diameter four flute cutter will remove about 1.2 cubic inches per minute of material from Ti5553 before the tool separates from the spindle taper. If the radial depth of cut is increased to remove more stock, the upper range 8,500 inch-pounds will be exceeded. Latest generation machines feature tool taper interfaces, such as Kennametal's KM4X, that can handle up to 35,000 inch-pounds of tool taper moment loads to accommodate long tools cutting highly resilient materials with a horizontal machining centre. These elements provide the advantages to push the tool through these tough materials. These power mechanisms are designed so as not influence the low frequency excitation conditions.
The ‘Titanium Triangle'
Other ‘must haves' in a hard metal machining system include adequate chip control, high-pressure coolant, and the right cutting tools as mentioned. There are some massive older-generation, triple spindle, high horsepower vertical machines that have been on factory floors for 25 years, making hard metal components fairly successfully. However, they are using cobalt-coated carbide cutting tools that require maintenance and regrinding. Further, since they are cutting in the vertical mode, the chips are often remachined. Plus the work area is wide open; high pressure coolant application is out of the question.
New machines specifically designed for hard metal parts have a horizontal spindle orientation. The chips fall to the bottom of the machine, and the work area is completely enclosed to flush coolant through the spindles at high pressures. Adequate flooding aimed at the cutting edge contributes to long tool life significantly. Also, cobalt tools are easing out of the scenario and being replaced by new generation indexable carbide cutters, which offer high stock removal rates and eliminate the regrinding maintenance of the colbalt coated cutters.