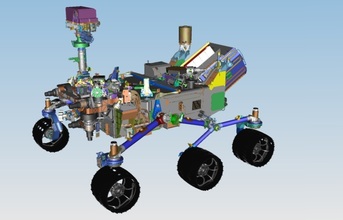
Rover Deployed Side - CAD
Parallel computing
Given the complexity of, not just the design, but the environments and potential scenarios that may be encountered, it's equally vital that simulation and analysis can test as many different cases as possible. This also needs to be done in a timely manner.
Effective parallel processing means numerical simulation of the finite element model can be done more efficiently because it leverages the potential of multi-core and multi-processor machines, using ultra-fast solving.
Parallel computing can cut processing times by as much as 30 per cent compared to using single processor systems.
Conclusion
FEA of critical design components, at the early design stage and on the engineering change list, ensures that the design can meet deformation, stress, vibration and/or temperature specifications for the worst case configurations specified. This greatly enhances the overall quality of any product, but is absolutely vital in those scenarios where there is no room for failure.
Analysis results identify critical areas which carry the bulk of stresses caused by deformation or vibration, as well as less important areas in which material reduction may be possible. This generally means the number of prototypes required can be reduced and the costs can be minimised without jeopardising the project.
The right Femap allows engineers to virtually model components, assemblies or systems to determine behaviour under a given set of boundary conditions, and is typically used in the design process to reduce costly prototyping and testing, evaluate differing designs and materials, and for structural optimisation to reduce weight.
For mission critical projects, Femap can be used as the pre- and postprocessor. It uses the CAD model to generate meshes for a mathematical model and, after finite element analysis, extracts results and views the condition and state of the structure under the various load conditions.
It caters for all manner of composite and laminate designs, as well as beam modelling and finite element meshing. It provides this along with a rich and powerful visualisation tool.
When it comes to launching a telescope into space, landing a rover on Mars, or exploring the very bottom of the ocean, the cost of failure is immeasurable. Being able to automate and customise simulation processes ensures that the designs work perfectly and that everything goes according to plan. In short, when perfection is paramount, Femap helps deliver mission-critical success.
The author is Femap Marketing - Mainstream Engineering Software, Siemens PLM Software.
END